The Maintenance Maturity Model in Manufacturing is a framework designed to assess and elevate a company’s maintenance practices, optimize operations, and drive sustained success. Regulated manufacturers rely on this model to pave the way for enhanced productivity, cost savings, and overall excellence.
Where is your company’s maintenance software found in the maturity model spectrum? Let’s find out!
Demystifying The Maintenance Maturity Model
Conceived by Winston Ledet in 1999, the Maintenance Maturity Model offers a structured approach to managing assets throughout their lifecycle. The model delineates the various maturity levels of asset management to provide organizations with a roadmap for handling and maintaining assets to bolster productivity and enhance operational efficiency. There are five levels for companies to progress through: Reactive, Preventive, Condition-Based, Predictive, and Predictive.
Let’s break down each level in turn:
Each level represents a progressive stage in a manufacturer’s maintenance program evolution.
Level 1: Reactive Maintenance
Organizations operate under a reactive maintenance paradigm at the foundational level of maintenance maturity. Here, maintenance activities are triggered solely in response to asset failures, often leading to unplanned downtime and production interruptions.
An example of this level in manufacturing would be a factory where machinery is only repaired or serviced when it breaks down, resulting in costly downtime and lost productivity.
Level 2: Preventive Maintenance
The next stage heralds a shift towards preventive maintenance, where assets are maintained at pre-scheduled intervals to mitigate the risk of failure.
For instance, in a manufacturing facility adopting preventive maintenance, equipment undergoes regular inspections and servicing based on predetermined schedules. This proactive approach minimizes the likelihood of unexpected breakdowns and extends the lifespan of critical assets.
Level 3: Condition Based Maintenance
As organizations progress, they embrace condition-based maintenance, leveraging maintenance software and technology to anticipate asset issues before they occur.
An example of this level in manufacturing would involve the use of sensors to monitor equipment health in real time. By analyzing data trends, organizations can forecast potential failures and execute maintenance activities precisely when needed, optimizing operational efficiency, and minimizing downtime.
Level 4: Predictive Maintenance
Predictive maintenance is at the forefront of maintenance maturity. In this type of maintenance, advanced analytics and machine learning algorithms are employed to predict asset issues and prescribe optimal actions.
Imagine a manufacturing plant utilizing wireless vibration sensors and machine learning algorithms to detect early signs of bearing wear on critical machinery. Based on these insights, the system provides specific recommendations for maintenance, empowering maintenance professionals to make informed decisions and optimize asset performance.
Level 5: Prescriptive Maintenance
This is the pinnacle of maintenance maturity. It’s world-class maintenance, characterized by proactive approaches, strategic alignment, and the integration of key performance metrics. In a world-class manufacturing organization, maintenance strategies are seamlessly integrated with broader business objectives, driving continuous improvement and operational excellence.
For example, a world-class manufacturer may implement a comprehensive reliability-centered maintenance program, where activities are strategically prioritized based on asset criticality and performance metrics, ensuring optimal resource allocation and asset performance.
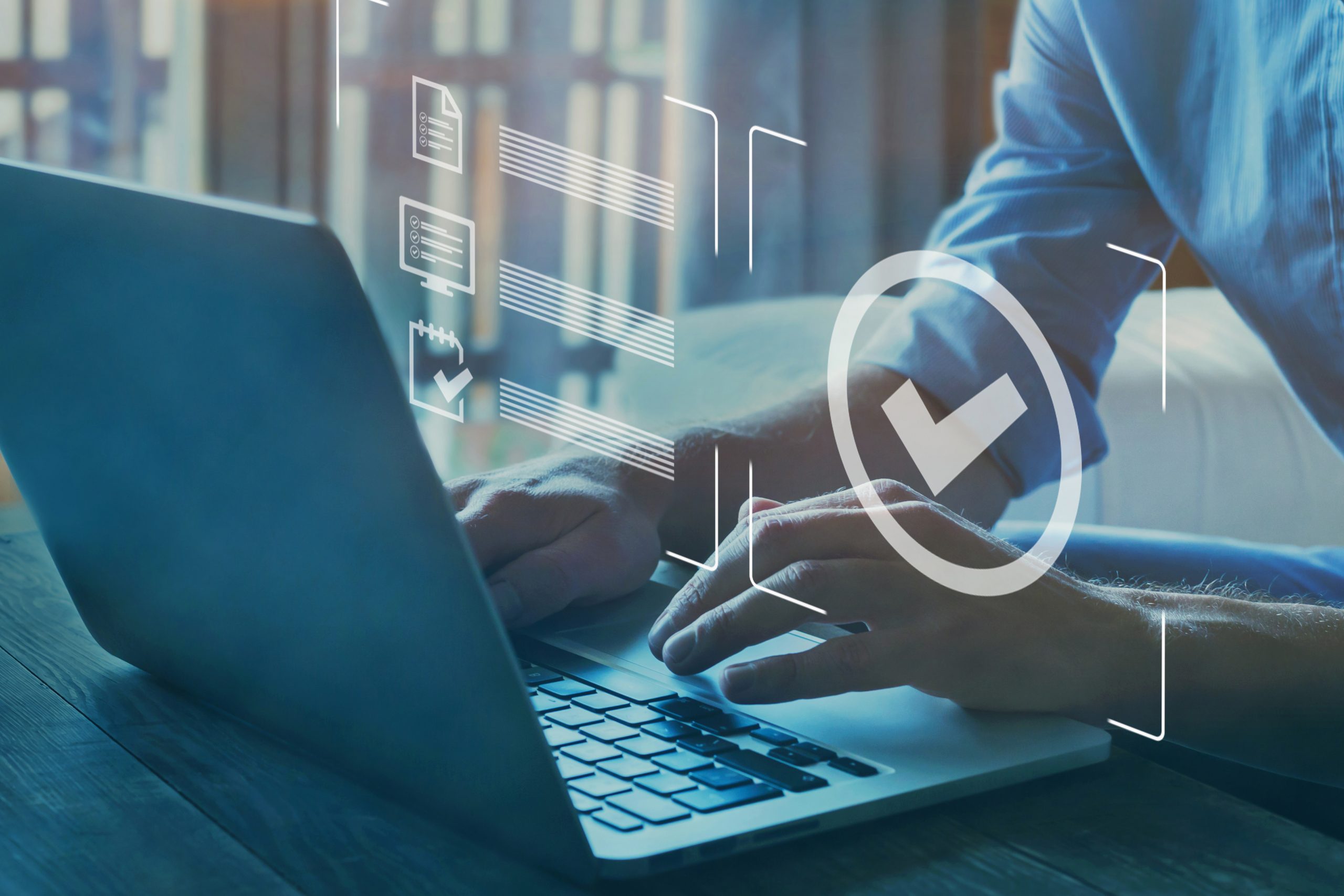
Why Mastering the Maintenance Maturity Model is Beneficial
The benefits of ascending the Maintenance Maturity Model come with both operational and financial advantages, including:
- Optimized Operational Performance: Proactive maintenance practices lead to optimized operational performance, resulting in higher throughput and reduced downtime. For example, a regulated manufacturer implementing predictive maintenance techniques can identify potential equipment failures before they occur, minimizing production interruptions and ensuring seamless operations.
- Cost Savings and Resource Optimization: By staying within labor and parts budgets, companies can optimize resource allocation and minimize expenditure. For instance, a manufacturer implementing a preventive maintenance schedule can extend the lifespan of critical equipment, reducing the need for costly replacements and repairs.
- Enhanced Product Quality and Customer Satisfaction: Improved maintenance practices translate to enhanced product quality and customer satisfaction. Picture a regulated manufacturer conducting regular equipment inspections and calibration checks—they can ensure product consistency and reliability, leading to improved customer satisfaction and loyalty.
- Market Adaptability and Agility: Embracing a mature maintenance model enables organizations to adapt quickly to changing market demands and technological advancements. If a manufacturer utilizing condition-based monitoring systems can detect shifts in equipment performance and adjust production processes accordingly, they can also ensure agility and competitiveness in the marketplace.
- Risk Mitigation and Compliance Assurance: Proactive maintenance reduces the risk of equipment failure and non-compliance with regulatory standards. When a regulated manufacturer implements a robust maintenance schedule, it can mitigate the risk of safety incidents and environmental violations, safeguarding employees and the environment while ensuring regulatory compliance.
The Maintenance Maturity Model is an accepted benchmark, a guiding beacon for regulated manufacturers for decades. It offers a structured approach to optimizing these practices and driving operational excellence.
By mastering this model and embracing continuous improvement, organizations can unlock its many benefits, ranging from optimized operational performance to enhanced product quality and customer satisfaction. And in today’s competitive landscape, ascending the Maintenance Maturity Model is not just a choice—it’s a strategic imperative.
So, after identifying your company’s position in this framework, how can you facilitate the necessary transformation and elevate your maintenance maturity?
Elevate Your Maturity with Maintenance Software
There are simple ways to elevate your maintenance maturity, and they hinge on adopting the right maintenance software to power your efforts.
First, you need to understand your maintenance maturity level. Explore the five levels of maintenance maturity defined above with your team. Assess your company on its responsiveness to world-class frameworks and explore the specific characteristics, challenges, and opportunities inherent to each level.
Compare your options to figure out how you’ll integrate maintenance software into your strategy. Recognize the crucial role technology will play in leveling up. Align potential software functionality with each maturity level to examine how each can help enhance automation, analytics, and optimization.
Evaluate the current status of your maintenance software and define objectives for change. Assessing current practices and aligning objectives with organizational goals will lay the groundwork for strategic improvements.
If you haven’t already done so, prepare reactive maintenance strategies to account for and swiftly address existing asset issues. And then leverage your maintenance software for streamlined operations that will set the stage for the proactive approaches that follow.
From there, we can transition to preventive maintenance. Once we’ve shifted to scheduled maintenance intervals, we can genuinely optimize preventive maintenance with automation provided by maintenance software to transition smoothly from reactive to preventive strategies.
Embracing predictive maintenance with your chosen solution comes next. This is where we’ll progress into predictive maintenance using data-driven decision-making, empowering it with maintenance software tools. We’ll strategically adopt predictive maintenance for optimal asset performance.
When prescriptive maintenance is in place, we’re ready to optimize. At this level, we employ advanced analytics and seamless maintenance software integration. The goal is to strategically utilize this software for operational excellence and integrate prescriptive maintenance into production strategies.
Achieving world-class maintenance excellence flows from prescriptive maintenance once you reach that level. It’s the highest level of maintenance maturity, where companies foster a proactive culture and strategically integrate maintenance software to achieve and sustain world-class maintenance.
It is crucial to continuously assess maintenance software effectiveness, incorporate user feedback, and strategically enhance efficiency with iterative improvement. This is not a “one-and-done” effort.
Progressing through these levels and embracing advanced maintenance strategies can help organizations unlock operational efficiency, minimize downtime, and drive sustained success. Fostering a culture of continuous improvement with an organizational ethos committed to embracing change and new technologies as they emerge will help your company stay ahead and maintain operational excellence. Reach out for a demo, and we’ll show you how maintenance software, and more specifically, a CMMS, facilitates this process!