Work order software is a pivotal tool in modern maintenance management, offering a comprehensive solution to streamline operations, enhance efficiency, and reduce downtime. But it’s much more than that. We’ll explore the definition, key features, and significance of work order software in contemporary manufacturing environments here.
Key Features of Work Order Software
Work order software represents an integrated management system designed to facilitate the execution of maintenance, inventory, and operational tasks across organizations from a centralized platform. Key features of work order software include:
- Work Order Management: Enables the creation, assignment, and tracking of work orders and work requests.
- Asset and Inventory Management: This function connects asset and parts records to streamline work processes and provide managers with insights into resource allocation.
- Real-Time Updates: Facilitates fast and streamlined communication among team members, enhancing collaboration and reducing delays.
- Reporting and Analytics: Provide robust reporting capabilities to track KPIs, analyze work order history, and identify areas for improvement.
- Configuration: Offers advanced configuration options to tailor the software to specific industry requirements and unique business processes.
The importance of work order software in modern maintenance management cannot be overstated. Here are some key reasons why it is indispensable:
- Enhanced Operational Efficiency: Work order software automates service requests, maintenance tasks, and work schedules, saving time and reducing manual workload.
- Improved Communication and Collaboration: By offering a centralized hub for information storage and retrieval, work order software fosters superior communication across departments and teams, ensuring smoother workflows.
- Increased Work Order Standardization: Digitizing work order processes minimizes the risk of human errors, ensures accurate task assignment and tracking, and improves overall precision.
- Optimized Resource Utilization: Work order software provides detailed insights into available resources and their deployment, enabling effective planning, minimizing waste, and cutting down on costs.
- Data-Informed Insights: Work order software facilitates data-informed decision-making by offering comprehensive data collection and helping identify performance trends and bottlenecks.
- Cost Savings: Work order software helps cut operational costs by increasing efficiency, reducing manual errors, optimizing resource utilization, and facilitating data-driven decisions.
Work order software is a cornerstone in modern manufacturing environments, offering a versatile solution to streamline maintenance management processes, enhance efficiency, and drive operational excellence.
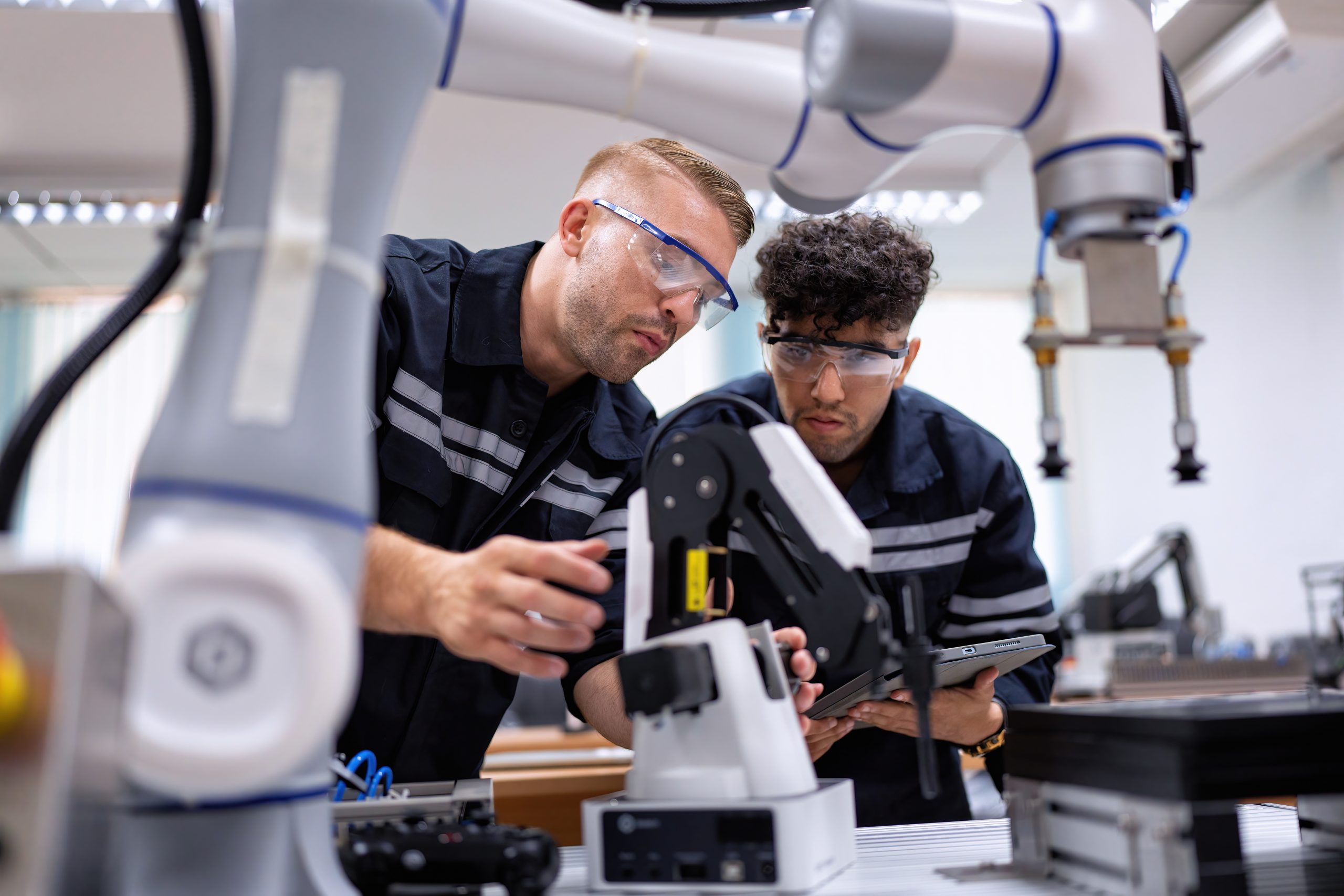
Challenges in Maintenance Management
Various maintenance management challenges exist, often stemming from traditional processes and the absence of a centralized work order system. Understanding these challenges is crucial for implementing effective solutions and streamlining maintenance operations.
Traditional maintenance processes in manufacturing are often plagued by several common pain points and inefficiencies, including:
- Manual Work Order Management: Reliance on manual methods, such as paper-based work orders or spreadsheets, leads to inefficiencies, errors, and delays in work order creation, assignment, and tracking.
- Lack of Standardization: The absence of standardized procedures and documentation results in inconsistent maintenance practices, which reduce reliability and increase the risk of equipment failure.
- Limited Visibility: Inadequate visibility into maintenance activities and asset performance hampers decision-making, hindering efforts to prioritize tasks, allocate resources efficiently, and plan preventive maintenance effectively.
- Communication Breakdowns: Poor communication among maintenance teams, technicians, and other stakeholders leads to misunderstandings, delays in task execution, and increased downtime.
- Reactive Maintenance: Over-reliance on reactive maintenance results in higher maintenance costs, increased downtime, and decreased equipment reliability.
The absence of a centralized work order system significantly impacts productivity and costs in manufacturing maintenance management:
- Increased Downtime: Without a centralized work order system, maintenance teams struggle to prioritize tasks effectively, leading to prolonged downtime and disruptions to production schedules.
- Resource Misallocation: Inefficient resource allocation due to the lack of visibility into maintenance activities results in wasted time, labor, and materials, driving up maintenance costs.
- Delayed Response to Issues: Manual work order management processes slow the response to maintenance issues, prolonging equipment downtime and reducing overall productivity.
- Higher Maintenance Costs: Reactive maintenance practices, coupled with inefficient work order management, lead to higher maintenance costs due to emergency repairs, unplanned downtime, and excessive labor expenses.
- Ineffective Planning and Scheduling: Without a centralized system for work order management, planning and scheduling preventive maintenance tasks become challenging, leading to missed inspections and increased risk of equipment failures.
The lack of a centralized work order system exacerbates common pain points and inefficiencies in traditional maintenance processes, resulting in decreased productivity and higher maintenance costs for manufacturing facilities. Implementing a robust work order software solution is essential for overcoming these challenges and streamlining maintenance management in manufacturing.
Key Features & Benefits of CERDAAC’s Work Order Software
CERDAAC’s Work Order Software offers a comprehensive solution for streamlining maintenance management in manufacturing environments. We help manufacturing facilities optimize their maintenance operations and achieve sustainable growth.
Our work order software facilitates seamless creation, assignment, and tracking of work orders, eliminating manual processes and reducing administrative burden. With intuitive interfaces and customizable workflows, maintenance teams can efficiently manage tasks and prioritize maintenance activities.
It provides real-time visibility into maintenance operations, allowing stakeholders to monitor progress, track performance metrics, and identify potential bottlenecks. Managers can make informed decisions and optimize resource allocation by gaining insights into work order status and asset health.
CERDAAC enhances communication and collaboration among maintenance teams. By facilitating seamless communication, the software ensures efficient task coordination and reduces response times to maintenance issues.
Robust asset management capabilities enable organizations to effectively track asset information, maintenance history, and performance data. Organizations can optimize asset lifecycle management and make data-driven maintenance decisions by maintaining comprehensive records.
By streamlining maintenance processes and improving asset visibility, CERDAAC’s Work Order Software enhances productivity and reduces downtime in manufacturing facilities. With proactive maintenance planning and predictive analytics, organizations can minimize equipment failures and maximize uptime.
Customizable work order forms and templates allow organizations to tailor workflows to their specific requirements. By adapting forms and templates, organizations can standardize processes, capture relevant data, and ensure compliance with industry regulations. It seamlessly integrates with asset management and inventory systems, enabling organizations to synchronize data across multiple platforms. Organizations can streamline operations, improve data accuracy, and enhance decision-making by centralizing information.
CERDAAC’s Work Order Software supports comprehensive asset life cycle management, from procurement to retirement. By tracking assets throughout their life cycle, organizations can optimize maintenance strategies, minimize costs, and extend asset lifespan. It’s a powerful solution for streamlining maintenance management in manufacturing environments. By leveraging its key features and benefits, organizations can improve operational efficiency, reduce downtime, and achieve long-term success.

Work Order Software Improves Safety and Compliance
Work order software significantly improves safety and compliance in manufacturing environments by providing tools and features to enforce standardized procedures and regulatory requirements. Organizations can ensure that maintenance tasks adhere to safety protocols and compliance standards through customizable work order forms and templates.
This documentation of maintenance activities, including safety inspections and equipment certifications, ensures thorough record-keeping for audits and regulatory compliance. By centralizing safety-related information and facilitating real-time communication, work order software enhances visibility into safety practices and enables timely response to safety incidents, ultimately fostering a safer work environment for employees and mitigating compliance risks.
Ensuring User Adoption & Training for Successful Implementation
User adoption and training are critical for successfully implementing work order software in manufacturing facilities. While work order software offers a wide range of features and benefits, its effectiveness relies on users’ willingness to embrace the new technology and integrate it into their daily workflows.
To ensure successful adoption, organizations should invest in comprehensive training programs to familiarize users with the software’s functionalities and train them on best practices for work order management. Additionally, providing ongoing support and soliciting feedback from users can help address any challenges or resistance to change. By prioritizing user adoption and training, organizations can maximize the value of work order software and drive successful outcomes in maintenance management.
Future Trends in Work Order Management
Future trends in work order management are expected to focus on leveraging advanced technologies such as artificial intelligence (AI) to optimize maintenance processes and improve operational efficiency. AI-powered maintenance optimization algorithms can analyze historical maintenance data, equipment performance metrics, and environmental factors to predict maintenance needs and optimize maintenance schedules dynamically.
By harnessing AI-driven insights, organizations can identify patterns, trends, and anomalies in maintenance data, enabling predictive decision-making and proactive maintenance strategies. Today’s work order software can automate repetitive tasks, optimize resource allocation, and provide actionable recommendations for continuous improvement, and AI will enhance these capabilities. As AI continues to evolve, its integration into work order management systems is poised to revolutionize maintenance practices and drive innovation in manufacturing operations.
Work order software serves as a cornerstone for streamlining maintenance management in manufacturing. It offers a comprehensive solution to address operational challenges, enhance safety and compliance, and unlock future opportunities for optimization and innovation. Reach out for a CERDAAC demo today, and we can show you how it looks in action!