Every minute counts in the manufacturing operations landscape, and downtime can lead to significant financial losses. Implementing a planned maintenance system is essential, yet it’s often mismanaged because not all maintenance strategies are created equal. Unfortunately, reactive maintenance is a common practice that often results in costly surprises and unplanned interruptions to production.
Let’s get to the heart of efficiency and reliability by exploring strategic planning and its impact.
Understanding the Impact of a Planned Maintenance System
Planned maintenance, or preventive maintenance, is a proactive approach to equipment upkeep. It involves scheduling regular inspections, tasks, and servicing of assets before they fail. The essence of planned maintenance lies in its ability to anticipate and address issues before they disrupt operations.
Businesses can face staggering downtime costs, but strategically planned maintenance programs offer a beacon of hope amidst daunting figures. By reducing unplanned downtime and enhancing productivity, planned maintenance becomes a linchpin for improving bottom lines. It comes down to being proactive instead of reactive.
Planned Maintenance Versus Reactive Maintenance
Reactive maintenance, often dubbed unplanned maintenance, involves addressing issues as they arise. While this approach provides immediate solutions, it can lead to inflated costs and extended downtime.
On the other hand, planned maintenance operates on a different paradigm.
In planned maintenance, the focus shifts from reacting to issues to proactively preventing them. Regular inspections, timely servicing, and adherence to maintenance schedules become the norm. This proactive stance reduces unexpected breakdowns and facilitates better budget control and resource allocation.
Consider a scenario: a critical piece of machinery breaks down unexpectedly. In a reactive maintenance scenario, the ensuing rush to repair, while effective in the short term, removes resources from other potentially time critical activities, ultimately leading to operational inefficiencies and increased costs. However, with a well-implemented planned maintenance system, such breakdowns become rare.
Regular servicing and timely interventions ensure that equipment remains in optimal condition, minimizing the risk of unexpected failures.
Core Elements of a Planned Maintenance System
What are the essential components a well-crafted, planned maintenance system?
1. Detailed Asset Inventories
Establish comprehensive asset inventories. This involves cataloging all equipment, machinery, and infrastructure critical to operations. Each asset should be meticulously documented, including its specifications, maintenance history, and future maintenance requirements. By clearly understanding all assets within the facility, maintenance teams can prioritize tasks effectively and ensure no equipment is overlooked.
2. Maintenance Schedules
Once assets are inventoried, the next crucial component is the development of maintenance schedules that outline the frequency and scope of maintenance tasks required for each asset. Whether it’s routine inspections, lubrication schedules, or component replacements, having a predefined maintenance schedule ensures that maintenance activities are conducted in a timely manner, reducing the risk of unexpected breakdowns and prolonging asset lifespan.
3. Role of Technology
In today’s digital age, technology is pivotal in facilitating planned maintenance systems. Computerized Maintenance Management Systems (CMMS) solutions provide a centralized platform for asset management, maintenance scheduling, and work order management. CMMS streamlines maintenance workflows, automates task assignments, and provides real-time visibility into maintenance activities.
Moreover, leveraging technologies such as IoT sensors and predictive analytics enables predictive maintenance strategies, where equipment health is monitored in real-time, and potential failures are predicted before they occur. By harnessing the power of technology, manufacturing facilities can transition from reactive to proactive maintenance practices, ultimately optimizing operational efficiency and reducing maintenance costs.
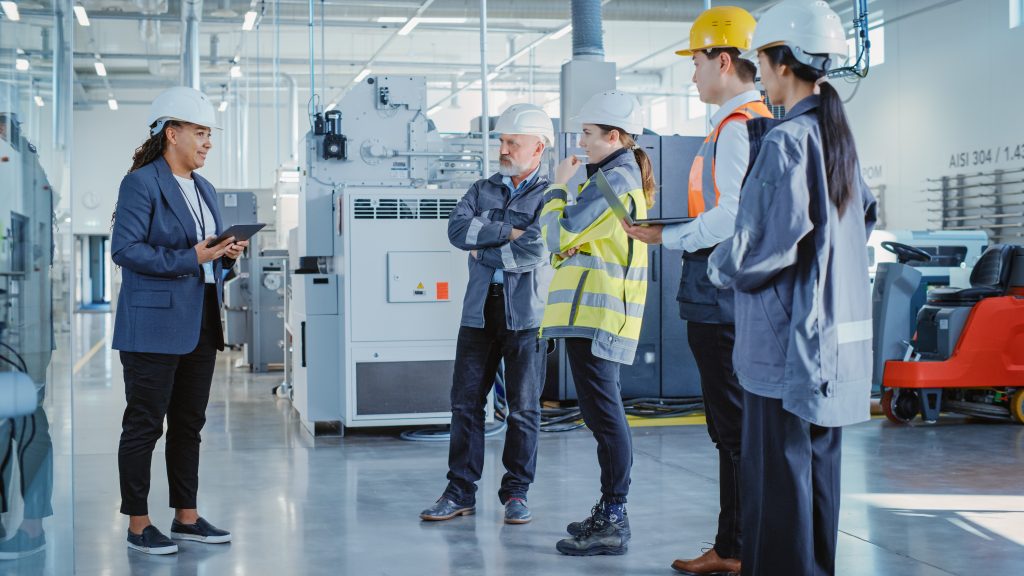
Types of Planned Maintenance Activities
Planned maintenance encompasses a spectrum of maintenance strategies, each tailored to meet specific operational needs and asset requirements. Let’s delve deeper into some of the key types of planned maintenance activities:
1. Preventive Maintenance
Preventive maintenance or planned preventive maintenance (PPM), involves scheduled maintenance activities performed at predetermined intervals to prevent equipment failures and prolong asset lifespan.
Examples of preventive maintenance include routine inspections, lubrication, and component replacements based on manufacturer recommendations or historical performance data. Preventive maintenance is particularly suitable for assets with predictable failure patterns or critical roles in operations.
2. Condition-Based Maintenance
Condition-based maintenance (CBM) focuses on monitoring the actual condition of equipment to determine when maintenance should be performed. Instead of relying on fixed schedules or predictive models, CBM utilizes sensor data and performance metrics to assess equipment health and trigger maintenance actions when predefined thresholds are met.
Condition-based maintenance allows for a more customized and adaptive approach to maintenance, as maintenance activities are performed based on the real-time condition of the asset rather than predetermined schedules or predictions.
3. Predictive Maintenance
Predictive maintenance leverages data and analytics along with AI to monitor trends and predict when equipment failure is likely, allowing maintenance activities to be performed only when necessary. By monitoring equipment health indicators such as temperature, vibration, and operating conditions in real time, predictive maintenance enables maintenance teams to detect anomalies and intervene before failures occur. This approach minimizes unnecessary maintenance and maximizes equipment uptime, making it ideal for assets where unplanned downtime poses significant risks or costs.
Choosing the Right Planned Maintenance Strategy
Selecting the appropriate maintenance strategy depends on various factors, including asset criticality, operational demands, available resources, and data availability.
Preventive maintenance is well-suited for assets with known failure patterns or where maintenance tasks can be performed efficiently at scheduled intervals. On the other hand, predictive maintenance offers a more data-centric approach, which is ideal for assets with complex failure modes or where unplanned downtime carries significant consequences.
Condition-based maintenance balances preventive and predictive approaches, offering flexibility and adaptability based on real-time equipment conditions. Embracing these core elements and leveraging technology-enabled solutions, businesses can optimize maintenance practices, enhance asset reliability, and drive operational excellence. And that’s just the start of the advantages.
Advantages of Implementing a Planned Maintenance System
Implementing a planned maintenance system is not just about avoiding unexpected breakdowns or reducing downtime; it’s a strategic investment that yields a multitude of direct and indirect benefits, ultimately paving the way for enhanced efficiency and cost savings across the board.
One of the most immediate and tangible benefits of a planned maintenance system is, of course, cost reduction. Organizations can significantly decrease repair and replacement expenses by proactively maintaining equipment and addressing issues before they escalate into costly failures. Moreover, planned maintenance helps optimize asset lifespan, reducing the frequency of expensive equipment purchases and extending the return on investment (ROI) for capital assets.
Then, we have its impacts on downtime: Downtime is the enemy of productivity in manufacturing. Unplanned equipment failures can bring production to a standstill, resulting in lost revenue, missed deadlines, and disgruntled customers.
A well-executed planned maintenance system minimizes the risk of unplanned downtime by keeping equipment in optimal working condition and addressing potential issues before they disrupt operations. This proactive approach preserves production continuity and enhances overall equipment effectiveness (OEE) and throughput.
Safety is also paramount in any manufacturing environment, and planned maintenance is crucial in ensuring a safe working environment for employees.
Regular equipment inspections and maintenance activities help identify and mitigate potential safety hazards, reducing the risk of accidents, injuries, and occupational health issues. By prioritizing safety through proactive maintenance practices, organizations demonstrate their commitment to employee well-being and compliance with regulatory standards.
A well-maintained and reliable equipment infrastructure fosters a positive work environment and boosts team morale. When employees can rely on equipment to perform as expected without constant disruptions or breakdowns, they feel more empowered and motivated to achieve their goals.
Planned maintenance instills a sense of ownership and pride among maintenance teams. This is helpful as they are critical in keeping operations running smoothly and efficiently.
Positive environmental impacts are also present, as efficient operations align with sustainability and environmental responsibility. A planned maintenance system promotes energy efficiency, resource conservation, and waste reduction by optimizing equipment performance and minimizing unnecessary energy consumption. By reducing the environmental footprint of manufacturing operations, organizations contribute to a healthier planet and enhance their reputation as socially responsible corporate citizens.
But how does one choose the right planned maintenance software?
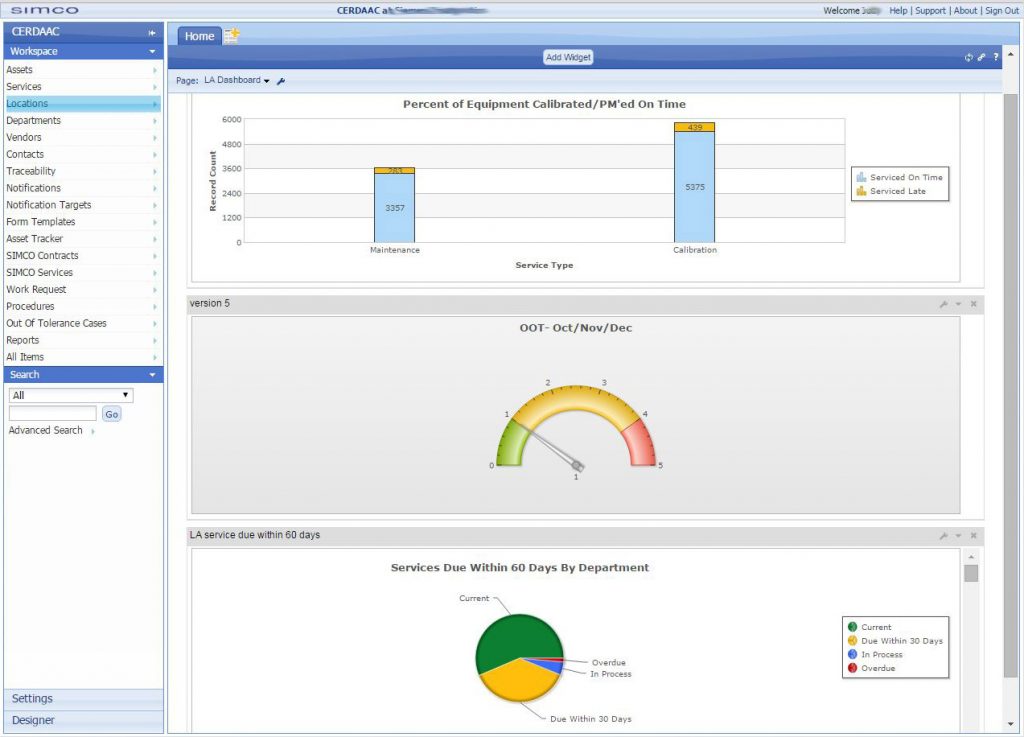
Choosing the Right Planned Maintenance Software
Choosing the right planned maintenance software is crucial for streamlining maintenance workflowsand maximizing asset performance.. But what features and functionalities should organizations look for when selecting a maintenance software solution?
When evaluating planned maintenance software options, organizations should consider factors such as scalability, ease of use, vendor reputation, and support services. It’s essential to assess the system’s compatibility with existing infrastructure and its ability to accommodate future growth and evolving maintenance needs.
And don’t forget configurability, which is also key in modern manufacturing environments. You’ll also want robust automated notifications and overall ease of use.
Additionally, involving key stakeholders from maintenance, operations, and IT departments in the selection process ensures that the chosen system aligns with the organization’s specific requirements and strategic objectives.
Innovative Asset Tracking and Maintenance Approaches
From Internet of Things (IoT) sensors to Artificial Intelligence (AI) algorithms, innovative solutions are changing how organizations manage their maintenance operations.
The integration of IoT sensors and AI algorithms is revolutionizing planned maintenance systems, enabling organizations to shift from reactive to proactive maintenance strategies. IoT sensors collect real-time data on equipment condition, performance, and environmental factors, providing valuable insights into asset health and potential failure risks. AI algorithms analyze this data to predict equipment failures before they occur, allowing maintenance teams to take preventive action and avoid costly downtime.
Efficient maintenance planning improves operational efficiency and contributes to environmental sustainability. Organizations can reduce their environmental footprint and support sustainable manufacturing practices by optimizing resource use, reducing waste, and minimizing energy consumption through proactive maintenance practices. From extending the lifespan of equipment to reducing energy-intensive maintenance activities, every aspect of planned maintenance plays a role in promoting environmental stewardship.
No two industries are alike, and maintenance requirements vary significantly based on factors such as equipment type, operating conditions, and regulatory standards.
Customizing maintenance plans and software solutions to fit industry needs is crucial for ensuring optimal asset performance and compliance. Whether it’s adapting maintenance schedules to accommodate seasonal demand fluctuations or incorporating industry-specific regulations into maintenance procedures, customization is key to success in planned maintenance implementation.
And maintaining high levels of data security and compliance with industry regulations is paramount in today’s interconnected world. Planned maintenance systems help organizations comply with industry standards and maintain data security through robust access controls, encryption protocols, and regular audits.
By safeguarding sensitive maintenance data and ensuring compliance with regulatory requirements, organizations can mitigate risks and build trust with customers, partners, and regulatory authorities.
Anticipating Future Planned Maintenance Trends
As the adage goes, “An ounce of prevention is worth a pound of cure.” With planned maintenance, organizations can mitigate the risks associated with unexpected equipment failures and create a more efficient and resilient manufacturing ecosystem.
The future of maintenance planning holds exciting possibilities. Emerging technologies such as augmented reality (AR), digital twins, and blockchain are poised to reshape the maintenance landscape, offering new opportunities for optimizing asset performance and driving operational excellence. By staying ahead of the curve and anticipating future maintenance trends, organizations can position themselves for success in an increasingly competitive market.
To see how a CMMS can help drive efficiencies in your maintenance operations, reach out to us for a demo of our award winning CERDAAC platform.