Equipment maintenance logs play a crucial role in ensuring the smooth operation and longevity of machinery in manufacturing. Unfortunately, many businesses do not manage these logs well.
These systematic records document all maintenance activities performed on equipment, providing a comprehensive history essential for various asset management aspects. The primary purpose of these logs is to track the history of repairs, inspections, and maintenance actions, ensuring that machinery operates efficiently and reliably. Accuracy is critical.
At the core of an effective equipment maintenance log is information. This includes essential identifiers such as the equipment’s name, model number, serial number, and location. Each maintenance activity is meticulously recorded with the date and time, providing a chronological upkeep history.
Maintenance actions form another critical component of the logs. Each entry specifies the type of maintenance performed—whether preventive, corrective, or predictive. A detailed description of the work carried out ensures a clear record of what was done and can be invaluable for future reference.
Additionally, the spare parts used during maintenance are carefully documented. This includes a list of replaced or repaired components, along with their part numbers and information about the suppliers. Such detailed records help track parts usage and manage inventory effectively.
The logs also record observations made during maintenance activities. Technicians’ name, notes and comments provide insights into the condition of the equipment before and after maintenance. These observations can highlight potential issues that need attention and ensure that equipment is always in optimal working condition.
Benefits of Maintaining Accurate Equipment Maintenance Logs
Maintaining accurate equipment maintenance logs offers numerous benefits that significantly enhance asset management in manufacturing.
One of the primary advantages is the ability to schedule preventive maintenance tasks more effectively. By having a clear record of when equipment was last serviced, asset managers can plan future maintenance activities efficiently. This proactive approach helps prevent unexpected breakdowns, reduce downtime, and extend the lifespan of the equipment.
Accurate maintenance logs also facilitate faster failure diagnosis and repair processes. A detailed history of maintenance activities enables technicians to identify patterns of failures or recurring issues quickly. This information can speed up the diagnosis and repair process, minimizing operational disruptions and increasing productivity.
Better decision-making for asset replacement is another significant benefit. Maintenance logs provide essential data on the performance and reliability of equipment over time. Asset managers can use this information to make informed decisions about when to replace aging or underperforming assets, ensuring optimal operational efficiency and cost-effectiveness.
Moreover, these logs help reduce inventory and operational costs. By tracking the usage and replacement of parts, companies can manage their inventory levels more effectively. This reduces excess stock, lowers inventory costs, and minimizes operational disruptions due to unavailable parts.
Another critical benefit of maintaining accurate maintenance records is increased asset safety and compliance. These logs ensure equipment is maintained according to safety standards and regulatory requirements. This enhances workplace safety and ensures compliance with industry regulations, reducing the risk of accidents and legal issues.
And finally, accurate maintenance logs can improve the resale value of assets. Well-maintained equipment with a documented care and maintenance history is more attractive to prospective buyers. This transparency makes the equipment more trustworthy and can result in a higher resale value.
Best Practices for Creating and Maintaining Equipment Maintenance Logs
Creating and maintaining accurate equipment maintenance logs requires adherence to best practices that ensure consistency, reliability, and usability of the data recorded. Here are some of the best practices to follow:
Standardizing Log Templates Across Assets
Standardizing log templates across all assets is essential to ensure uniformity and ease of use. Standardized templates facilitate consistent data entry, making comparing and analyzing maintenance records across different equipment easier. These templates should include fields for general information, maintenance actions, parts used, and observations.
Defining Clear Processes for Data Entry and Record-Keeping
Clear processes for data entry and record-keeping are crucial for maintaining accurate maintenance logs. Establishing guidelines for how and when data should be recorded ensures that all relevant information is captured promptly and accurately. This includes specifying who is responsible for data entry, the data types to be recorded, and the format in which data should be entered.
Ensuring Regular Updates and Data Accuracy
Regular updates to maintenance logs are vital for keeping records current and accurate. Scheduled reviews and updates should be part of the maintenance routine to ensure that all activities are documented. Implementing checks and audits can help verify the accuracy of the data and identify any discrepancies that need correction.
Leveraging Technician Feedback for Continuous Improvement
Technicians who perform maintenance tasks can provide valuable insights into the logging process. Regularly soliciting feedback from technicians can help identify areas where the process can be improved, ensuring that the logs are comprehensive and user-friendly. This feedback can also highlight recurring issues or inefficiencies in the maintenance process.
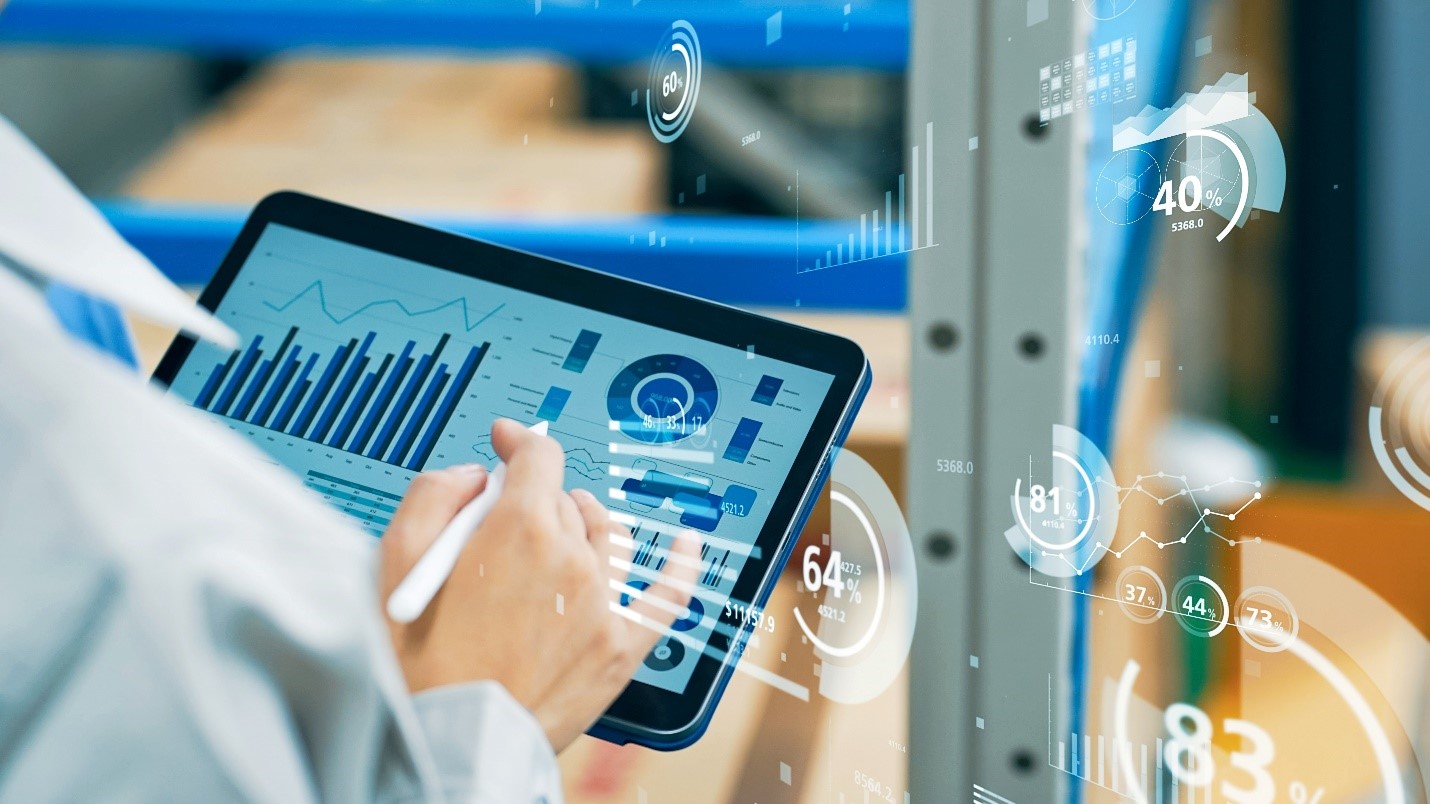
Using CERDAAC to Streamline Log Management and Automate Data Entry
Leveraging tools like CERDAAC can significantly streamline the management of maintenance logs. CERDAAC is a comprehensive CMMS platform that standardizes and automates data entry, reducing the manual workload for technicians and ensuring greater accuracy in the records. It also provides centralized storage for all maintenance data, making accessing and analyzing information easier.
Leveraging Equipment Maintenance Logs for Optimization
Equipment maintenance logs are not just records but valuable tools for optimizing maintenance operations and overall asset management. Asset managers can identify trends and patterns in equipment performance and failures by analyzing maintenance history. This analysis can reveal recurring issues, peak failure times, and other critical insights that can inform maintenance strategies and prevent future breakdowns. Digital logs greatly facilitate this type of analysis.
Historical maintenance data is invaluable for optimizing preventive maintenance schedules. By understanding the typical lifespan and failure points of components, maintenance activities can be scheduled more effectively to prevent unexpected failures. This ensures that maintenance is performed just-in-time, avoiding both over- and under-maintenance.
Maintenance logs that include detailed records of parts used can greatly improve inventory management. By tracking the usage and lifespan of spare parts, asset managers can better forecast future needs and ensure that the right parts are available when needed. This reduces downtime caused by waiting for parts and minimizes the costs of holding excess inventory.
Enhancing Overall Maintenance Strategy and Decision-Making
Comprehensive maintenance logs provide a wealth of data that can enhance the overall maintenance strategy and decision-making process. This data helps asset managers make informed decisions about equipment repairs, replacements, and upgrades. It also supports the development of long-term maintenance plans that align with organizational goals and improve operational efficiency.
These logs enable better scheduling, faster diagnostics, informed decision-making, and ultimately, a more efficient and reliable maintenance program.
CERDAAC: The Ultimate Solution for Equipment Maintenance Log Management
CERDAAC stands out as a leading solution for managing equipment maintenance logs, offering a range of features designed to simplify and enhance the maintenance process. Some of the key features include:
– Centralized Data Storage: All maintenance data is stored in a centralized location, making it easily accessible for analysis and reporting.
– Customizable Templates: CERDAAC provides customizable log templates, allowing asset managers to standardize data entry across all assets.
– Real-Time Updates: The platform supports real-time updates, ensuring that all maintenance activities are promptly recorded and available for review.
– Advanced Reporting and Analytics: CERDAAC offers powerful reporting and analytics tools that help asset managers track performance metrics, identify trends, and make data-driven decisions.
CERDAAC simplifies the management of equipment maintenance logs through automation and user-friendly features. The platform’s automated data entry capabilities ensure that maintenance activities are logged accurately and promptly, minimizing the risk of human error. With real-time updates, technicians can input data directly from the field, ensuring that logs are always current.
The centralized data storage provided by CERDAAC allows asset managers to access all maintenance records from a single location. This makes retrieving historical data, analyzing maintenance trends, and generating detailed reports easy. The customizable templates ensure that all relevant information is captured consistently, facilitating easier comparison and analysis across different assets.
CERDAAC’s advanced reporting and analytics tools provide valuable insights into maintenance performance. Asset managers can track key performance indicators (KPIs), such as Mean Time Between Failures (MTBF) and Mean Time to Repair (MTTR), to assess the effectiveness of maintenance strategies and identify areas for improvement.
Businesses Transform Their Maintenance Operations with CERDAAC
Many businesses have successfully transformed their maintenance operations using CERDAAC. For instance, a large manufacturing company struggling with frequent equipment failures and downtime implemented CERDAAC to streamline its maintenance processes. The company reduced downtime and improved overall equipment efficiency by automating log management and leveraging the platform’s analytics tools.
Another example is a pharmaceutical manufacturer that needs to comply with stringent regulatory requirements for equipment maintenance. By adopting CERDAAC, the company ensures accurate and timely documentation of all maintenance activities, facilitating compliance with regulatory standards and enhancing operational efficiency.
Equipment Maintenance Logs are a Must
Maintaining accurate and detailed equipment maintenance logs is fundamental to effective asset management in manufacturing. These logs enable easier scheduling of preventive maintenance tasks, better decision-making for asset replacement, reduced inventory and operational costs, and increased asset safety and compliance.
Adopting best practices is essential to fully realizing the benefits of equipment maintenance logs. Companies need to standardize log templates, define clear data entry processes, ensure regular updates, leverage technician feedback, and utilize digital tools like CERDAAC. By following these practices, asset managers can enhance the accuracy and utility of maintenance records, leading to more efficient and effective maintenance operations.
Experience the Benefits Firsthand
Implementing CERDAAC can streamline log management, automate data entry, and provide powerful insights into maintenance performance. Reach out for a demo to experience the transformative benefits firsthand and explore how easy it can be to optimize maintenance strategies, improve equipment reliability, and achieve greater operational efficiency.