Computerized Maintenance Management Systems (CMMS) are instrumental in transforming traditional maintenance operations into highly efficient, streamlined processes. These systems automate and coordinate the maintenance of equipment, assets, buildings, and infrastructure, providing a significant upgrade over traditional manual methods that are often cumbersome and error-prone.
What Exactly is a CMMS, and How Does It Differ from Traditional Maintenance Management Methods?
A CMMS is software that simplifies a company’s equipment, assets, and facility maintenance activities. Unlike traditional methods that rely heavily on paper records and reactive maintenance approaches, a CMMS provides a centralized digital hub for managing maintenance tasks. This shift not only facilitates a more proactive maintenance strategy but also enhances overall operational efficiency by reducing downtime and extending the lifespan of equipment.
CMMS systems are foundational for achieving operational excellence because they significantly improve maintenance efficiency and asset management. Industries such as manufacturing, healthcare, and utilities rely on CMMS to ensure their equipment operates reliably and without unscheduled downtimes. By leveraging real-time maintenance capabilities, CMMS helps organizations to preemptively address potential issues, thus minimizing disruptions and optimizing performance.
These systems contribute to better resource management, cost reduction, and compliance with industry standards, all of which are critical components of operational excellence. Integrating CMMS with other enterprise systems (like ERP and IoT devices) further enhances its value, providing comprehensive insights that drive better decision-making and strategic planning across the organization.
The Evolution of CMMS Software
The origins of CMMS can be traced to the 1960s, with the adoption of early computer systems by large manufacturing firms. Initially, these systems utilized simple databases on mainframe computers to track maintenance tasks, which marked a significant departure from the previous manual processes.
Maintenance management has historically been a complex field requiring precise coordination and efficient management of resources. Initially, organizations relied on paper-based systems to schedule and document maintenance tasks, which, as mentioned, was time-consuming and error-prone.
As industrial operations grew in complexity and scale, the limitations of manual methods became increasingly apparent. There was a pressing need for more reliable, scalable, and efficient systems to handle the critical functions of maintenance management.
The introduction of personal computers and local area networks in the 1980s and 1990s significantly transformed maintenance management practices. These technologies facilitated more sophisticated data management and easier communication between maintenance teams, paving the way for the first true CMMS solutions. These systems enabled maintenance managers to schedule, track, and document maintenance activities more efficiently than ever before.
Key Technological Advancements Propelled CMMS Growth
Several key technological advancements have been instrumental in the evolution of CMMS, including:
- Database Technology: Early CMMS solutions leveraged database technology to organize and store large amounts of maintenance-related data. This allowed for more systematic tracking of maintenance schedules, asset histories, and inventory levels.
- Internet and Cloud Computing: With the advent of the internet and later, cloud computing, CMMS solutions expanded their capabilities significantly. Cloud-based CMMS platforms offered greater scalability, accessibility, and cost-effectiveness, eliminating the need for on-premise hardware and enabling real-time data access across geographically dispersed locations.
- Integration Capabilities: Modern CMMS solutions often feature robust integration capabilities with other enterprise systems such as Enterprise Resource Planning (ERP) and the Internet of Things (IoT). These integrations facilitate a more holistic view of maintenance data, automate data collection, and enable advanced analytics to predict maintenance needs.
- Artificial Intelligence and Machine Learning: The latest advancements in AI and machine learning are beginning to be integrated into CMMS platforms. These technologies can analyze vast amounts of maintenance data to identify trends, predict failures before they occur, and recommend optimal maintenance schedules.
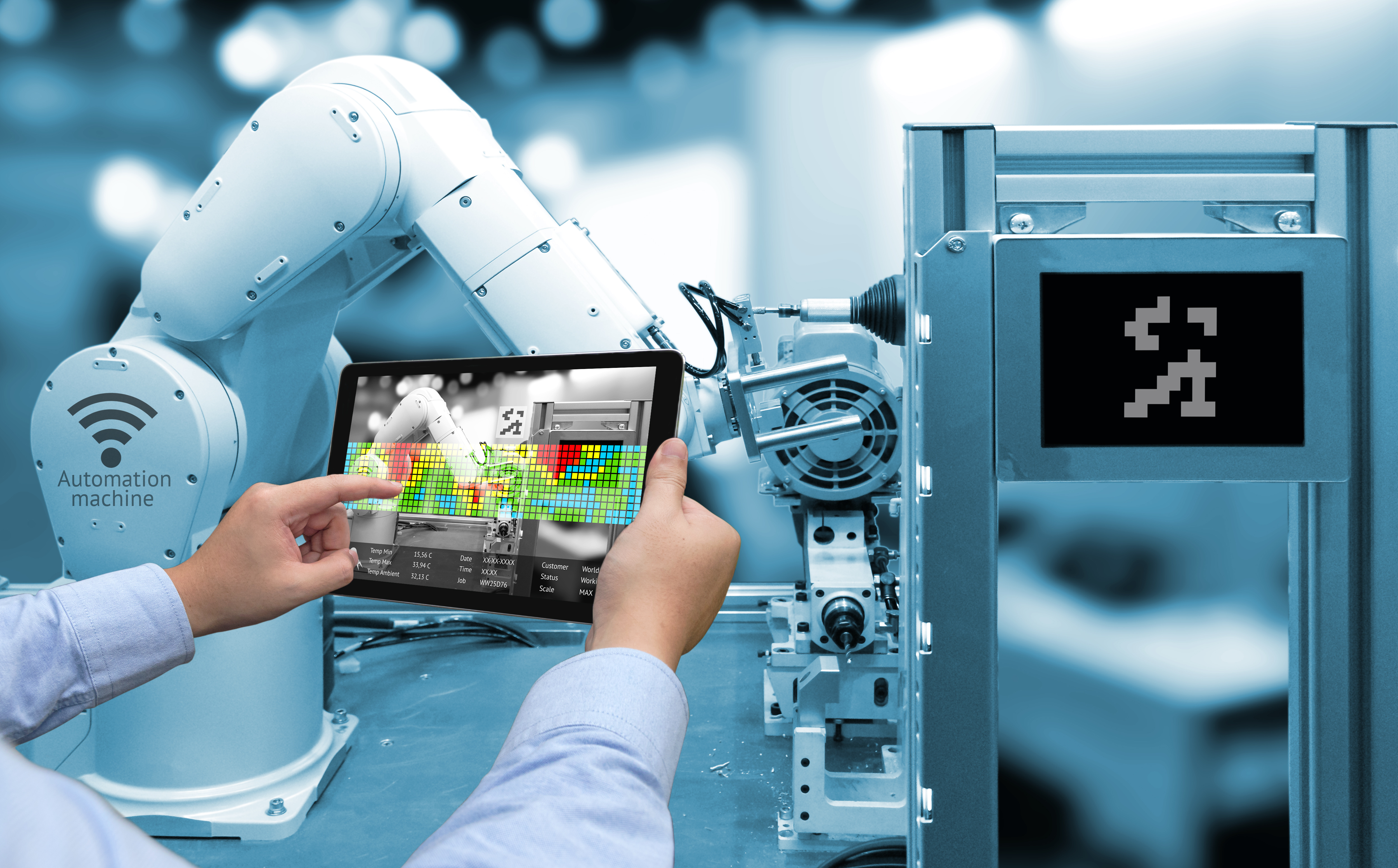
Exploring the Multifaceted Capabilities of CMMS
A CMMS transforms how maintenance activities are planned, executed, and monitored within manufacturing environments. These systems offer a range of functionalities that streamline maintenance operations and provide critical insights that help make informed operational decisions. Below, we delve into the essential functions of a CMMS and explore how they contribute to more efficient maintenance management.
How a CMMS Facilitates Critical Functions, Like Work Order Management
Work order management is one of the core functions of any CMMS. This feature allows maintenance managers to create, assign, track, and close work orders electronically, ensuring that every task is accounted for and completed on time. This automation significantly reduces the likelihood of missed maintenance activities and ensures that all tasks are performed as scheduled, which is crucial in a manufacturing setting where equipment uptime is directly tied to productivity and revenue.
The critical nature of this function lies in its impact on operational reliability and efficiency. Efficient work order management helps prioritize maintenance tasks based on their urgency and impact, thereby reducing equipment downtime and optimizing maintenance resources.
A comprehensive asset database within a CMMS is a game-changer for maintenance management. It includes detailed information on each asset, such as its maintenance history, part specifications, warranty details, and operational guidelines. Having all this information centralized and accessible enhances maintenance efficiency in several ways:
- Proactive Maintenance: With detailed historical data, maintenance teams can move from a reactive to a proactive maintenance approach. Predictive maintenance, based on the asset’s history and performance data, can be implemented to address potential issues before they lead to equipment failure.
- Reduced Downtime: A proactive approach to maintenance prevents unplanned production stopages due to equipment failure and significantly reduces downtime.
- Compliance and Reporting: Ensuring compliance with industry standards and generating accurate maintenance reports becomes streamlined when all necessary asset data is readily available.
Inventory monitoring in CMMS plays a crucial role in minimizing costs and ensuring the availability of critical resources. This feature allows maintenance teams to track the usage rates of spare parts and supplies, automate reordering processes, and avoid overstocking, which ties up capital unnecessarily.
By having real-time visibility into inventory levels, companies can maintain the delicate balance between having enough inventory to avoid production disruptions and not so much that it leads to high carrying costs. And it helps reduce the losses associated with obsolete or expired items, optimizing the financial resources allocated to inventory.
Integrating CMMS with Other Enterprise Systems
The integration of CMMS with other enterprise systems, such as ERP (Enterprise Resource Planning) and IoT (Internet of Things) devices, is vital for a holistic approach to maintenance management. This integration offers several benefits:
- Data Consistency: Integrating CMMS with ERP systems ensures that data related to procurement, finance, and operations is synchronized, leading to consistent and accurate information across all departments.
- Enhanced Decision Making: Combining IoT device data with CMMS can provide maintenance managers with real-time data on equipment performance, enabling them to make immediate and informed decisions regarding maintenance needs and schedules.
- Automated Processes: Integration can automate various processes, such as work order creation when a fault is detected by an IoT device, streamlining the maintenance workflow and reducing human errors.
Adopting a CMMS contributes to cost savings in several key areas:
- Reduced Maintenance Costs: By enabling proactive and predictive maintenance strategies, CMMS helps avoid the costly repairs and replacements associated with unexpected equipment failures. Scheduled maintenance activities ensure that equipment is maintained at optimum levels, which minimizes the likelihood of downtime and extends the life of assets.
- Inventory Management: CMMS provides accurate tracking and management of spare parts and materials. This prevents overstocking and understocking scenarios, which can tie up capital or lead to emergency procurement at higher prices. Efficient inventory control directly reduces waste and improves the bottom line.
- Labor Optimization: CMMS enhances workforce productivity by organizing maintenance tasks more efficiently and reducing the time spent on each task. It also minimizes the need for overtime through better scheduling and planning, further reducing labor costs.
The impact of CMMS on equipment uptime is profound. By systematically scheduling preventive maintenance and facilitating swift responses to repair needs, CMMS minimizes the frequency and duration of downtime. Increased equipment uptime directly translates to higher production capacities and more consistent output, which are critical for maintaining a competitive advantage in manufacturing.
And by ensuring that equipment runs at peak efficiency, CMMS also helps improve the overall productivity of the manufacturing process by automating manual processes that traditionally consume significant time and resources like work order and inventory management.
CMMS Enhances Workplace Safety & Compliance with Regulatory Standards
CMMS can store and manage safety procedures, ensuring they are followed during maintenance operations. This includes locking out and tagging out equipment to prevent accidental operation while maintenance is performed. And organizations can keep detailed records of all maintenance activities, which is crucial for meeting regulatory standards and passing audits. The system can alert managers to upcoming inspections or maintenance tasks critical for compliance.
By facilitating regular maintenance and ensuring all equipment operates correctly, CMMS reduces the likelihood of accidents caused by equipment failure. This protects employees and reduces the risk of costly legal issues related to workplace safety.
In conclusion, implementing CMMS in manufacturing environments offers substantial benefits beyond simple maintenance management. By enhancing operational efficiency, improving safety, and ensuring compliance, CMMS supports manufacturing organizations in achieving higher productivity and operational excellence.
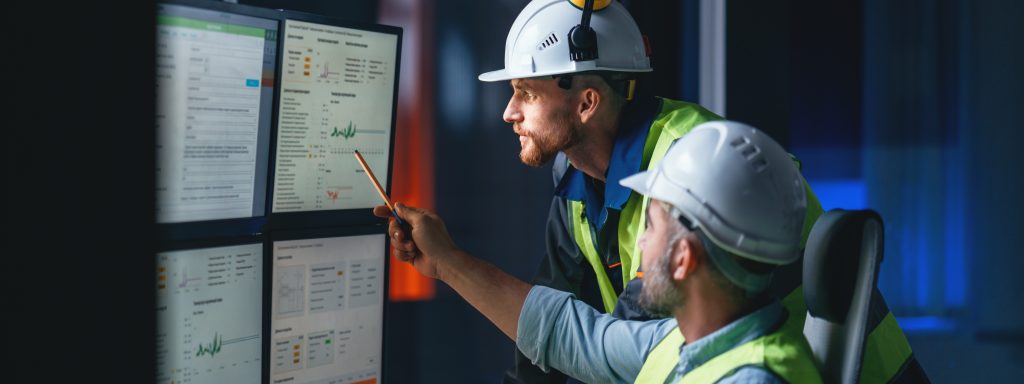
Choosing the Right CMMS Software
The choice of a CMMS can significantly impact the effectiveness of your maintenance strategies, the efficiency of your maintenance operations, and overall asset lifecycle costs. Here’s how to navigate this selection process for optimal results.
Look for a CMMS that tracks every asset, including its maintenance history, performance metrics, and repair schedules. This will enable proactive maintenance and lifecycle management.
The system should allow for easy creation and monitoring of work orders, with capabilities to attach documents, images, and instructions. This is essential for scheduling, assigning, tracking, and reporting on maintenance tasks. Effective inventory management tools help track parts and supplies, manage reordering, and forecast future needs based on usage trends.
And robust reporting tools are crucial for analyzing maintenance data and tracking KPIs to optimize operations and reduce costs.
Scalability in a CMMS is essential for ensuring that the system can grow along with your organization. A scalable CMMS can handle increasing amounts of data and more complex operations without performance degradation. As your organization expands, whether by acquiring more assets, increasing workforce size, or expanding operational scope, the CMMS should be able to accommodate these changes without requiring a complete system overhaul. This adaptability prevents disruptions and supports continuous improvement in maintenance processes.
The user interface (UI) should be intuitive and user-friendly. A complicated interface can deter users from fully adopting the system. Test the UI in a demo or trial to ensure it meets your usability standards.
Check what training and support are offered by the CMMS provider. Comprehensive training and responsive customer support are crucial for smooth implementation and ongoing use.
And the ability to customize the software according to specific needs is vital. The CMMS should allow for adjustments in workflows, forms, and reports to align with your operational practices.
Lastly, consider feedback from current users of the CMMS. User reviews can provide insights into the software’s reliability, performance, and how well it meets the needs of similar organizations.
The Future of CMMS Maintenance: The Next Wave of Innovations
The integration of the Internet of Things (IoT) and Artificial Intelligence (AI) technologies are setting the stage for a new era, enhancing CMMS capabilities and providing unprecedented levels of predictive maintenance and operational efficiency. It enables systems to predict and prevent equipment failures before they disrupt operations.
IoT devices can monitor various conditions in real-time, from temperature and pressure to vibrations and power consumption. When this data is fed into a CMMS enhanced with AI, the system can analyze patterns and predict when maintenance should be performed. This preemptive approach allows maintenance teams to address potential issues before they escalate into costly repairs or operational downtime.
AI algorithms improve with each interaction, learning from historical data to refine their predictive capabilities. This increases the accuracy of maintenance schedules and helps optimize resource allocation, thereby enhancing the overall efficiency and lifespan of equipment.
And a CMMS with predictive capabilities can schedule maintenance tasks based on data insights and prioritize them according to their urgency and impact on production. By minimizing the risk of unexpected equipment failures, predictive maintenance not only saves costs but also improves safety and reduces the environmental impact of manufacturing processes.
Mastering CMMS Maintenance in Manufacturing is essential for enhancing operational efficiency, increasing equipment reliability, and managing maintenance costs effectively. Integrating modern technologies such as IoT and AI into CMMS solutions propels these systems into a new era of maintenance management and transforms them into crucial tools for predictive maintenance and advanced data analytics.
As manufacturing processes become increasingly complex, the importance of implementing a robust CMMS cannot be overstated. Organizations seeking to maintain competitive advantage and operational excellence will find that investing in a sophisticated CMMS solution is a step toward achieving these objectives and driving significant, long-term business value. Be sure to reach out for a demo to see our CMMS in action today!