In a world where precision drives progress, calibration is a critical enabler of accuracy, efficiency, and safety. Industries, from manufacturing to healthcare to energy production, rely on calibration to ensure that their measurement devices perform as expected. But what exactly is calibration, and why is it so essential?
What is Calibration?
At its core, calibration is the process of comparing the performance of a measurement device (such as a thermometer, scale, or pressure gauge) against a recognized standard. The goal is to ensure the device provides accurate and reliable readings, enabling organizations to operate confidently.
Imagine a pharmaceutical drug manufacturing plant. If a temperature sensor used in production gives an inaccurate reading, the entire batch could be compromised, leading to waste, regulatory issues, or, worse, risk to human health. Calibration prevents such risks by aligning devices with known standards, ensuring correct and reliable measurements.
Why is Calibration Important?
Reducing Measurement Errors
Measurement errors can cause a domino effect of problems, from faulty products to increased costs and even safety hazards. For example, in the energy sector, an uncalibrated meter might inaccurately measure energy output, leading to disputes over billing and loss of customer trust. Regular calibration helps organizations catch and correct these errors before they escalate.
Ensuring Compliance with Industry Standards
Industries like healthcare, aerospace, and pharmaceuticals operate under strict regulatory frameworks, such as ISO and FDA guidelines. Calibration is a cornerstone of compliance, demonstrating that an organization maintains quality and adheres to safety standards. Companies risk hefty fines or, worse, losing certification without proper calibration records.
Enhancing Safety in Critical Environments
Specific industries, such as nuclear energy and healthcare, demand absolute accuracy due to the high stakes. For example, uncalibrated medical devices can lead to misdiagnosis or improper treatment, jeopardizing patient safety. Calibration ensures these devices deliver reliable data, safeguarding lives.
Calibration is a structured process designed to ensure measurement devices perform accurately and reliably. Each step in the process is crucial for maintaining operational consistency and compliance with industry standards. Let’s break it down into four main stages:
1. Assessment
The first step is identifying which equipment requires calibration. Not all devices need calibration at the same frequency, so this stage involves evaluating usage patterns, criticality, and the manufacturer’s recommendations. Additionally, acceptable tolerance levels for each device are defined, specifying the range within which the device’s readings are considered accurate.
For example:
- Machines operating in high-precision production lines in a manufacturing plant may require frequent calibration compared to less critical devices.
- In a hospital, diagnostic tools like MRI machines or patient monitors are prioritized for calibration to ensure patient safety.
2. Comparison
Once identified, the device’s performance is tested against a recognized standard. This comparison occurs under controlled conditions to eliminate external factors that could impact the results. The standard used may vary depending on the device type but must be traceable to an authoritative reference, such as those set by national metrology institutes.
For instance:
- A torque wrench in an automotive plant might be tested against a certified load cell to ensure it applies the correct amount of force.
- In a laboratory, a pipette’s volume delivery is compared to a gravimetric or photometric standard.
3. Adjustment
If discrepancies are identified during the comparison stage, the device undergoes adjustments to bring it back within acceptable tolerance levels. This step ensures the device can deliver accurate readings moving forward. Sometimes, if a device cannot be adjusted, it may need to be replaced or retired.
For example:
- A pressure gauge showing deviations may have its internal components recalibrated to restore accuracy.
- A faulty meter might be recalibrated in energy systems using advanced software tools to ensure correct data logging.
4. Documentation
The final stage is recording all calibration activities, results, and adjustments. Detailed documentation serves multiple purposes:
- Ensures compliance with industry standards and audits (such as ISO/IEC 17025).
- Provides a historical record for future reference or trend analysis.
- Demonstrates a commitment to quality control during certifications or inspections.
For example:
- A medical laboratory maintains monthly records of calibrations for its blood analyzers, ensuring accuracy for clinical diagnostics.
- A manufacturing plant creates calibration logs for torque wrenches, proving adherence to ISO quality management requirements.
Calibration is not just a technical task—it’s a business-critical process. Each stage is meticulously designed to ensure operational excellence, enhance safety, and maintain compliance in an increasingly regulated world.
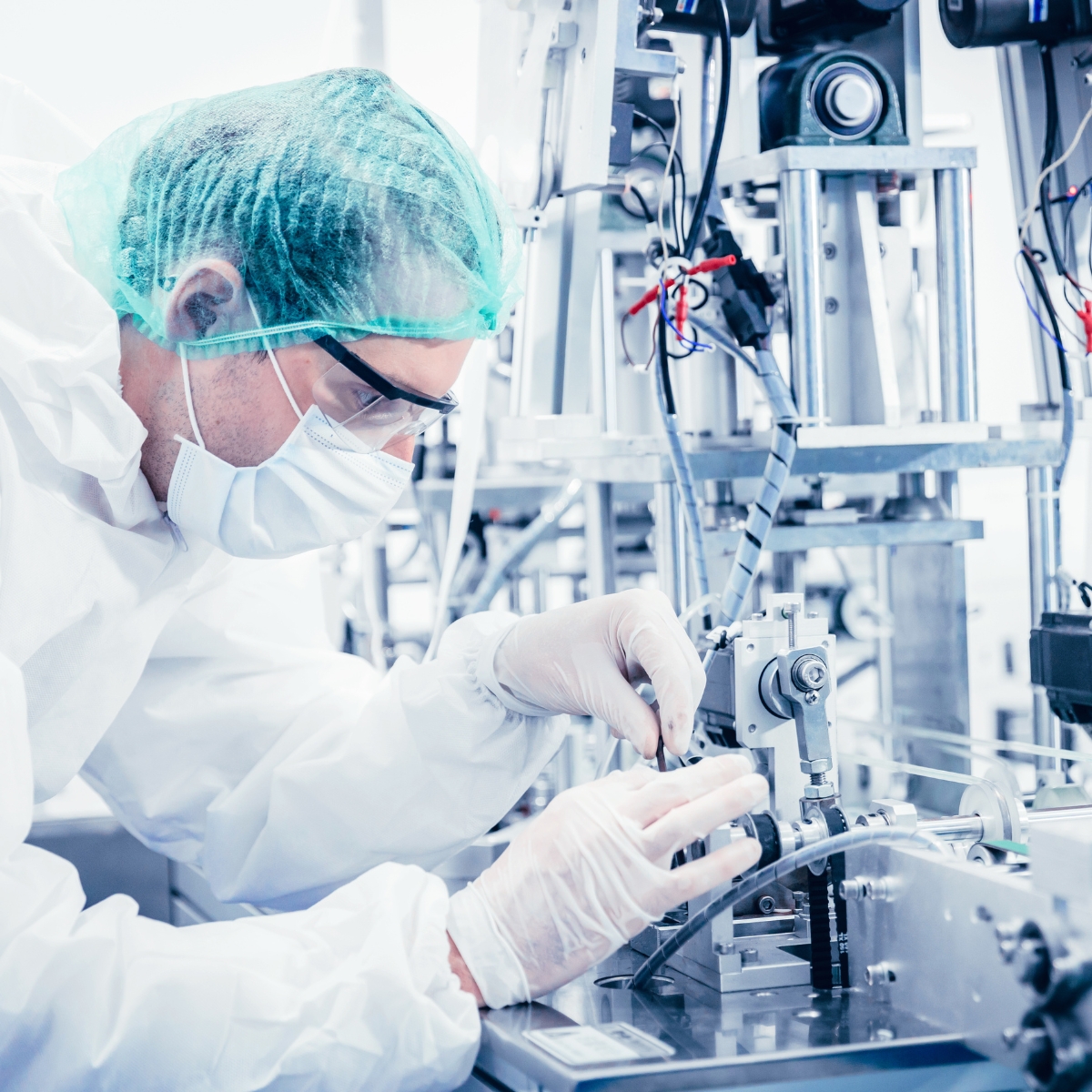
How Calibration Impacts Operations
To truly understand the importance of calibration, consider this flowchart:
- Accurate Measurements → 2. Improved Product Quality → 3. Regulatory Compliance → 4. Operational Efficiency → 5. Cost Savings
This cycle illustrates how calibration creates a ripple effect, influencing every aspect of operations. But more specifically, let’s speak to the key features and benefits of calibration:
Key Features
- Asset Monitoring: Tracks the calibration status of all equipment, alerting users when devices are due for recalibration.
- Preventative Maintenance: Integrates calibration schedules with maintenance workflows to detect issues early.
- Compliance Reporting: Automatically generates detailed reports to meet regulatory requirements.
Key Benefits
Increased Operational Safety
In environments where safety is paramount, such as chemical plants or hospitals, accurate measurements can prevent catastrophic errors. Calibrated instruments provide peace of mind that operations are running safely.
Compliance with Industry Standards
Compliance is not just about avoiding fines; it’s about building trust. Calibration ensures that organizations meet regulatory requirements, reinforcing their commitment to quality and safety.
Cost Savings
Measurement errors can lead to costly product recalls, production downtime, or safety incidents. Regular calibration minimizes these risks, saving organizations money in the long run.
Leaders in Calibration Management
Manufacturing leaders who are recognized as pioneers in the calibration space prioritize:
- Measurement Accuracy: Ensuring devices deliver precise and repeatable readings.
- Compliance Support: Offering tools that simplify adherence to rigorous industry standards.
Integrated calibration solutions streamline workflows for complex industries like oil and gas, with handheld equipment offering portability and precision for on-site applications.
CERDAAC Calibration Cloud offers unique advantages, including:
- Tailored Solutions: Explicitly designed for asset-heavy industries like life sciences and manufacturing.
- Advanced Reporting: CERDAAC’s software goes beyond calibration, integrating compliance reporting with broader asset management.
- Comprehensive Integration: Seamlessly connects calibration to maintenance schedules, reducing redundancy and enhancing efficiency.
CERDAAC empowers organizations to treat calibration as a regulatory necessity and a strategic asset. Calibration is more than a technical requirement—it’s a competitive advantage. Contact us today to schedule a personalized demo and discover how our calibration software can elevate your compliance, safety, and efficiency and ensure long-term success in a competitive world.