Scheduled maintenance refers to any pre-planned maintenance work that must be completed by a specific person or group within a set timeframe. Getting this right isn’t as easy as it sounds, as the sheer volume of tasks to track can be overwhelming. And missing required maintenance results in unplanned downtime, with associated costs.
Tasks to track include replacing air filters, performing oil changes, conducting routine inspections, and other maintenance activities that occur at regular intervals. These tasks can either be part of a recurring schedule or one-off planned actions to ensure equipment reliability and performance.
By adhering to a regular maintenance schedule, manufacturers can prevent sudden equipment failures that disrupt production processes, leading to significant cost savings and enhanced operational efficiency. For example, regularly changing the bearings on a conveyor belt every 30 days can prevent a catastrophic failure that would halt production lines and incur high repair costs.
It’s important to plan maintenance and schedule it. While the terms ‘scheduled maintenance’ and ‘planned maintenance’ are often used interchangeably, they have distinct meanings in the context of maintenance activities.
- Planned maintenance refers to the comprehensive process of identifying maintenance tasks, gathering necessary tools, and establishing workflows to complete the tasks. It involves a strategic approach to determine what needs to be done, why it is necessary, and how it will be executed.
- However, scheduled maintenance focuses on the specific timing and assignment of these tasks. It involves setting deadlines, assigning responsibilities, and ensuring that the maintenance work is performed at regular intervals. Scheduled maintenance can be a component of a broader planned maintenance strategy or a standalone practice to manage routine tasks.
Here are a couple of examples to illustrate the differences:
– Planned Maintenance: Developing a predictive maintenance program that uses sensors and data analysis to forecast when equipment will need servicing based on usage patterns and performance indicators.
– Scheduled Maintenance: Setting up a calendar reminder for a technician to replace an air filter in a machine every three months, regardless of its current performance, to ensure continuous operation
Scheduled maintenance is an essential practice for manufacturers looking to reduce downtime and improve efficiency and support long-term operational success.
Benefits of Implementing a Scheduled Maintenance Program
Scheduled maintenance significantly enhances the reliability of equipment and increases uptime. By regularly performing maintenance tasks such as inspections, lubrication, and part replacements, potential issues are identified and addressed before they lead to equipment failure.
For example, conducting routine lubrication and filter replacements ensures that machines operate smoothly, reducing the likelihood of unexpected breakdowns. This proactive approach minimizes downtime, allowing for continuous and efficient production processes.
One of the primary benefits of scheduled maintenance is the reduction in the risk of sudden equipment breakdowns. When maintenance is conducted at regular intervals, minor issues are detected early and corrected before they escalate into major problems.
This not only prevents costly repairs but also avoids the significant production losses associated with equipment downtime. For instance, scheduling regular inspections of conveyor belts can prevent them from mistracking. Preventing mistracking is essential, as even slightly misaligned conveyor belts can lead to spillage, excessive wear of the belt, and major damage to equipment or even the structure.
Scheduled maintenance extends the lifespan of assets by ensuring that they are consistently kept in optimal working condition. Regular servicing, such as tightening loose parts and replacing worn-out components, helps maintain the machinery’s functionality over a longer period.
Additionally, well-maintained equipment retains a higher resale value. Buyers are more likely to invest in second-hand machinery that has a documented history of regular maintenance, as it indicates that the equipment is reliable and less likely to experience frequent failures.
Implementing a scheduled maintenance program enhances workplace safety by reducing the likelihood of accidents caused by equipment malfunctions.
Regular maintenance ensures that all safety features are operational and that machinery meets industry safety standards. For example, routine checks on emergency stop mechanisms and safety guards prevent accidents during machine operation. And adhering to scheduled maintenance helps companies comply with regulatory requirements, avoiding penalties and ensuring a safe working environment for employees.
Overall, scheduled maintenance allows for more effective cost management by preventing unplanned downtime and reducing the need for emergency repairs. By planning maintenance activities in advance, companies can allocate resources more efficiently, scheduling maintenance during off-peak hours to minimize disruptions to production.
And a scheduled maintenance program enables better inventory management. Companies can keep track of necessary spare parts and materials, ensuring they are available when needed, avoiding delays in maintenance activities.
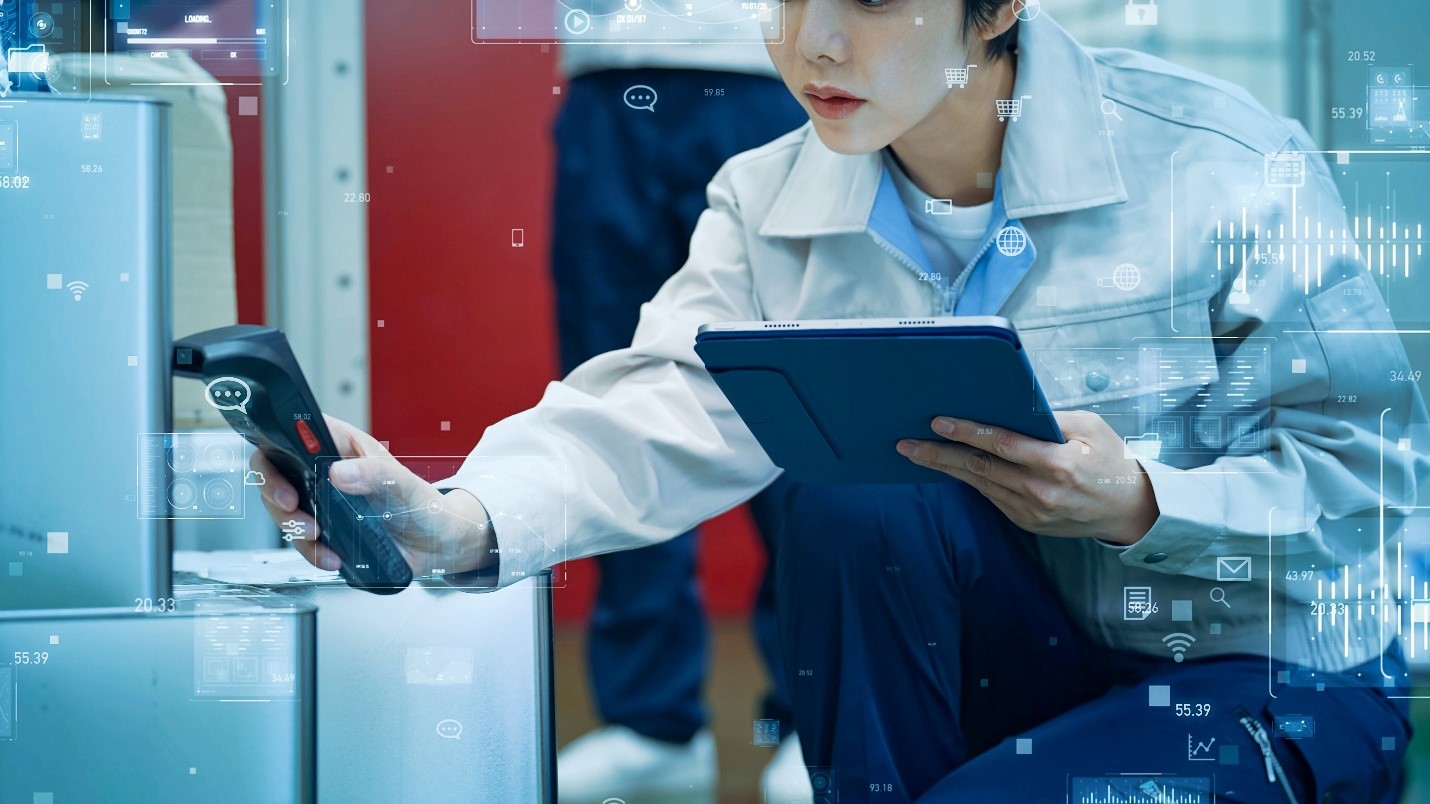
Best Practices for Effective Scheduled Maintenance Management
Developing a comprehensive maintenance schedule is the foundation of effective scheduled maintenance management. This involves:
- Manufacturer Recommendations: Adhering to the maintenance guidelines provided by equipment manufacturers ensures that assets are serviced at optimal intervals, which can prevent premature wear and tear.
- Asset Criticality: Prioritizing maintenance tasks based on the criticality of the assets to the production process. For example, machinery that is vital to production should have more frequent and detailed maintenance schedules compared to less critical equipment.
For example, if a manufacturer recommends changing the oil of a machine every 3,000 operational hours, this should be strictly incorporated into the maintenance schedule. For critical assets like a primary conveyor belt, inspections might be scheduled every two weeks to prevent any unforeseen failures.
Accurate tracking and documentation of maintenance activities are essential for ensuring that all scheduled tasks are completed and for identifying trends in equipment performance.
Manufacturers must keep detailed records of all maintenance tasks performed, including dates, technician names, and specific actions taken. Utilizing tracking tools and software to monitor maintenance activities helps ensure compliance with the schedule. This documentation provides a historical record that can be useful for troubleshooting recurring issues and is handy when it’s time for audits.
Computerized Maintenance Management Systems (CMMS) like CERDAAC offer powerful features for managing scheduled maintenance efficiently, hitting every high point:
- Scheduling: CMMS allows for the creation of detailed maintenance schedules and automated reminders.
- Assignment: Tasks can be assigned to specific technicians based on their skills and availability.
- Tracking: Real-time tracking of maintenance activities ensures that tasks are completed on time and potential issues are flagged promptly.
CERDAAC can be used to set up automatic reminders for upcoming maintenance tasks, assign these tasks to technicians, and track their completion in real-time. This helps in maintaining an organized and efficient maintenance workflow.
It also offers clear communication to technicians and stakeholders. Effective communication is crucial for the smooth execution of scheduled maintenance tasks, and CERDAAC helps with:
- Notifications: Sending automated timely notifications and reminders to technicians about upcoming maintenance tasks.
- Stakeholder Communication: Keeping stakeholders informed about scheduled maintenance activities, potential impacts, and expected downtime that might affect production.
Regular monitoring and optimization of scheduled maintenance programs ensures they remain effective and aligned with operational needs. For example, it allows manufacturers to review maintenance logs and CMMS reports quarterly to assess the effectiveness of the maintenance schedule. If certain assets require more frequent maintenance or if there are recurring issues, adjust the schedule and maintenance procedures to address these findings.
These practices ensure that maintenance is conducted proactively, reducing downtime, and extending the lifespan of critical assets.
Understanding Scheduled Maintenance Critical Percent (SMCP)
Scheduled Maintenance Critical Percent (SMCP) is a metric used to prioritize maintenance tasks based on their criticality and timeliness. SMCP helps maintenance teams identify which overdue tasks need immediate attention by providing a quantifiable measure of how late a task is relative to its scheduled occurrence.
This metric is crucial because it helps organizations manage their maintenance backlog efficiently, ensuring that the most critical tasks are addressed first to prevent equipment failures and unplanned downtime.
For example, in a manufacturing plant, if a machine that is vital to the production process has a maintenance task that is overdue by several days, calculating the SMCP can help the maintenance team prioritize this task over less critical ones, minimizing the risk of a significant production halt.
Calculating SMCP involves a straightforward formula that considers the number of days a maintenance task is overdue and the frequency of its maintenance cycle. The formula is as follows:
SMCP Formula: SMCP = (# days late + # days in cycle) / # days in cycle * 100
Steps to Calculate SMCP:
- Determine the Number of Days Late: Identify how many days past the scheduled date the maintenance task is.
- Identify the Maintenance Cycle: Establish the frequency of the maintenance cycle (e.g., every 30 days, 60 days, etc.).
- Divide your result by the number of days in the maintenance cycle and multiply that number by 100 to arrive at a percentage.
Example Calculations:
- Task A is on a 30-day maintenance cycle and is 3 days overdue – SMCP of 110%
- Task B is on a 60-day maintenance cycle and is 5 days overdue – SMCP of 108.33%
These calculations show that Task A has a slightly higher SMCP than Task B, so Task A should be prioritized.
Tracking SMCP offers several advantages that can enhance maintenance efficiency and reduce downtime:
- Improved Scheduling: By quantifying the criticality of overdue tasks, maintenance teams can make informed decisions about which tasks to address first. This ensures that the most critical tasks are not overlooked, leading to a more effective maintenance schedule.
- Reduced Reactive Maintenance: Regularly calculating and monitoring SMCP helps identify assets that frequently require attention, allowing teams to address underlying issues before they lead to unexpected failures. This proactive approach minimizes the need for reactive maintenance.
- Enhanced Auditing and Compliance: Keeping track of SMCP helps organizations maintain thorough records of maintenance activities, which is beneficial for internal audits and compliance with industry regulations. It ensures that critical maintenance tasks are not neglected and that maintenance schedules are adhered to.
- Better Resource Allocation: Understanding the criticality of tasks through SMCP enables better allocation of resources, such as assigning skilled technicians to the most critical tasks and ensuring that necessary parts and tools are available.
A manufacturing plant that consistently tracks SMCP can reduce equipment downtime by ensuring that the most critical maintenance tasks are always prioritized. This leads to fewer unexpected breakdowns and more efficient use of maintenance personnel and resources.
It’s an incredibly valuable metric for managing maintenance tasks effectively. By understanding its definition, calculating it accurately, and leveraging its benefits, organizations can improve their maintenance scheduling, reduce downtime, and enhance overall operational efficiency. Tracking SMCP ensures that maintenance activities are prioritized based on their criticality, leading to a more proactive and organized maintenance management approach.
Implementing Scheduled Maintenance with CERDAAC
CERDAAC is a powerful Computerized Maintenance Management System (CMMS) that offers a range of features designed to streamline and enhance scheduled maintenance management. Key features include:
- Automated Scheduling: CERDAAC allows users to create automated maintenance schedules, ensuring that tasks are planned well in advance and reminders are sent to relevant personnel.
- Work Order Management: The system facilitates the creation, assignment, and tracking of work orders, ensuring that maintenance tasks are efficiently managed from start to finish.
- Real-Time Tracking: Maintenance activities can be tracked in real-time, providing insights into task completion and any delays that may occur.
- Asset Management: CERDAAC offers robust asset management capabilities, allowing users to track the maintenance history and performance of each asset.
- Reporting and Analytics: Comprehensive reporting and analytics tools enable users to monitor maintenance performance, identify trends, and make data-driven decisions.
CERDAAC simplifies the creation, assignment, and tracking of scheduled maintenance tasks:
- Creation: CERDAAC simplifies the creation of maintenance schedules by allowing users to set up recurring tasks based on manufacturer recommendations and asset criticality. Users can input all necessary details, such as task descriptions, required materials, and estimated completion times.
- Assignment: Tasks can be easily assigned to specific technicians based on their skills, availability, and location. CERDAAC’s intuitive interface allows maintenance managers to see all pending tasks and assign them with just a few clicks.
If a technician specializing in conveyor systems is available, the system can assign all conveyor-related maintenance tasks to them, ensuring efficient use of expertise and resources.
- Tracking: Real-time tracking features allow maintenance managers to monitor the status of each task. They can see which tasks are in progress, completed, or overdue, and can take immediate action if there are any delays.
A maintenance manager can log into CERDAAC and see that a critical maintenance task is overdue. They can then reassign the task or follow up with the technician to ensure it is completed promptly.
Implementing an effective scheduled maintenance program with the help of CERDAAC can significantly improve operational efficiency and reduce downtime. We encourage readers to take the following steps to streamline their maintenance operations:
- Evaluate Your Current Maintenance Practices: Assess your existing maintenance processes and identify areas for improvement.
- Create a Comprehensive Maintenance Schedule: Develop a detailed schedule based on manufacturer guidelines and asset criticality.
- Monitor and Optimize Your Maintenance Program: Continuously review maintenance data and optimize your program based on performance metrics and feedback.
By adopting these practices and leveraging our capabilities, you can ensure that your maintenance operations are efficient, proactive, and aligned with industry best practices. Reach out for a demo today to elevate your scheduled maintenance strategy and achieve operational excellence.