Preventive maintenance is a proactive approach to maintaining the condition of equipment and assets by conducting regular inspections and upkeep. The primary goal of preventive maintenance is to prevent equipment failures before they occur, thereby reducing unplanned downtime and the costs associated with emergency repairs. This strategy ensures that machinery and equipment are kept in optimal working condition, maximizing productivity, enhancing safety, and extending the lifespan of assets.
A well-implemented preventive maintenance program can lead to substantial cost savings by reducing the frequency and severity of equipment failures, which often require expensive and time-consuming repairs.
Preventive maintenance is critical for operations because it minimizes unexpected breakdowns by planning maintenance activities in a systemized manner. By regularly servicing equipment, businesses can avoid the significant disruptions that reactive maintenance often brings.
The Shift from Reactive to Preventive Maintenance
Transitioning from reactive to preventive maintenance involves a systematic approach to changing how maintenance activities are planned and executed.
- Reactive maintenance, often referred to as “Break-Fix” involves fixing problems as they arise, which can lead to unplanned downtime and higher maintenance costs.
- On the other hand, preventive maintenance aims to address potential issues before they become significant problems.
The first step in this transition is establishing clear goals and priorities for the maintenance program. This involves identifying the most critical assets and determining the maintenance activities required to keep them in optimal condition. Businesses should also create a comprehensive preventive maintenance schedule, which can be based on time intervals or usage metrics, to ensure that maintenance tasks are performed regularly.
A Computerized Maintenance Management System (CMMS) is crucial in facilitating this shift.
A CMMS helps organizations streamline their maintenance processes by automating work orders, scheduling maintenance activities, and tracking asset performance. With a CMMS, maintenance teams can easily monitor the condition of equipment, plan maintenance tasks, and ensure that all necessary parts and resources are available. This level of organization and automation significantly enhances the efficiency and effectiveness of preventive maintenance programs.
Key Differences: Corrective vs. Preventive Maintenance
Corrective and preventive maintenance are two distinct approaches to maintaining equipment and assets. Corrective maintenance, also known as reactive maintenance, involves repairing equipment after failure. This approach is typically unplanned and can lead to extended downtime, increased repair costs, and potential safety hazards.
In contrast, preventive maintenance involves regularly scheduled inspections and servicing of equipment to prevent failures before they occur. This proactive approach ensures that machinery is kept in good working condition, significantly reducing the likelihood of unexpected breakdowns.
The advantages of prioritizing preventive maintenance over corrective maintenance are numerous:
- Reduced Downtime: Preventive maintenance minimizes the occurrence of unexpected equipment failures, ensuring that operations run smoothly without interruptions.
- Cost Savings: By addressing potential issues before they become serious problems, businesses can avoid the high costs associated with emergency repairs and prolonged downtime.
- Improved Safety: Regular maintenance reduces the risk of accidents and injuries caused by malfunctioning equipment, creating a safer working environment.
- Increased Asset Lifespan: Preventive maintenance helps in maintaining the optimal condition of equipment, thereby extending its useful life and delaying the need for costly replacements.
- Enhanced Productivity: With equipment running at peak performance, productivity levels are higher, and maintenance teams can focus on planned activities rather than emergency repairs.
- Improved Safety: Regular maintenance reduces the risk of accidents and injuries caused by malfunctioning equipment, creating a safer working environment.
A robust preventive maintenance plan is essential for manufacturers looking to enhance their operational efficiency, reduce costs, and improve safety.
Designing Your Preventive Maintenance Plan
Creating an effective preventive maintenance plan happens in seven steps:
- Assess Your Inventory: Before implementing a preventive maintenance plan, thoroughly assess all assets that require maintenance. This includes buildings, manufacturing equipment, company-owned vehicles, HVAC systems, and other miscellaneous assets. Categorizing these assets based on their criticality to your operations will help prioritize maintenance tasks.
- Identify Maintenance Tasks and Triggers: Document all necessary maintenance tasks for each asset. These tasks can be derived from the original equipment manufacturer’s (OEM) recommendations and the asset’s maintenance history. Identify triggers for these tasks based on time, usage, or condition. For instance, a task might be triggered every 100 hours of operation or every six months, depending on the asset’s requirements.
- Create Detailed Checklists: Develop comprehensive checklists for each maintenance task. These checklists should include all steps needed to complete the task, ensuring consistency and thoroughness across the maintenance team. Utilize input from experienced technicians to create accurate and practical checklists.
- Set Up Tools and Software: Implement tools to manage and document maintenance tasks. While some organizations start with pen and paper or spreadsheets, investing in a CMMS significantly enhances efficiency. A CMMS helps schedule tasks, track work history, and manage inventory.
- Train Your Team: Train your maintenance team on the new preventive maintenance plan and any associated software or tools. Ensure that all team members understand their roles and responsibilities, the importance of following checklists, and how to document their work accurately.
- Implement and Monitor: Roll out the preventive maintenance plan, starting with the most critical assets. Monitor the execution of the plan closely, collecting data on task completion, equipment performance, and any issues that arise. Use this data to make informed adjustments to the plan as necessary.
- Continuous Improvement: Regularly review and fine-tune your preventive maintenance plan. Conduct root cause analysis on any failures to improve maintenance tasks and triggers. Involve all stakeholders in this continuous improvement process to ensure the plan evolves with your operations’ changing needs.
Leveraging CMMS for Preventive Maintenance
Integrating CMMS software into your preventive maintenance strategies offers numerous benefits that streamline and enhance maintenance operations. CMMS software automates the scheduling of maintenance tasks based on predefined triggers such as time intervals or usage metrics. This ensures that all preventive maintenance activities are timely, reducing the risk of equipment failures.
CMMS systems simplify the creation, assignment, and tracking of work orders. Maintenance tasks can be prioritized based on criticality, and technicians can be assigned tasks based on expertise and availability. This leads to more organized and efficient maintenance operations.
It also helps manage spare parts inventory by tracking stock levels and usage. This ensures that necessary parts are always available for maintenance tasks, reducing downtime caused by waiting for parts.
These systems provide real-time data on maintenance activities, equipment performance, and resource utilization. This data is invaluable for making informed decisions, identifying trends, and improving maintenance strategies. Additionally, CMMS offers detailed reporting capabilities that help in tracking key performance indicators (KPIs) and measuring the success of the preventive maintenance plan.
A cloud-based CMMS enables seamless communication among maintenance teams, allowing them to share information and updates instantly. This reduces miscommunication and ensures everyone is on the same page regarding maintenance tasks and priorities. This information is useful for maintaining compliance with industry regulations by keeping accurate records of all maintenance activities. This includes documenting inspections, repairs, and certifications, which can be easily accessed during audits.
By automating scheduling, enhancing work order management, and providing real-time data, a CMMS transforms preventive maintenance into a more manageable and effective process, ultimately leading to reduced downtime, lower maintenance costs, and increased productivity.
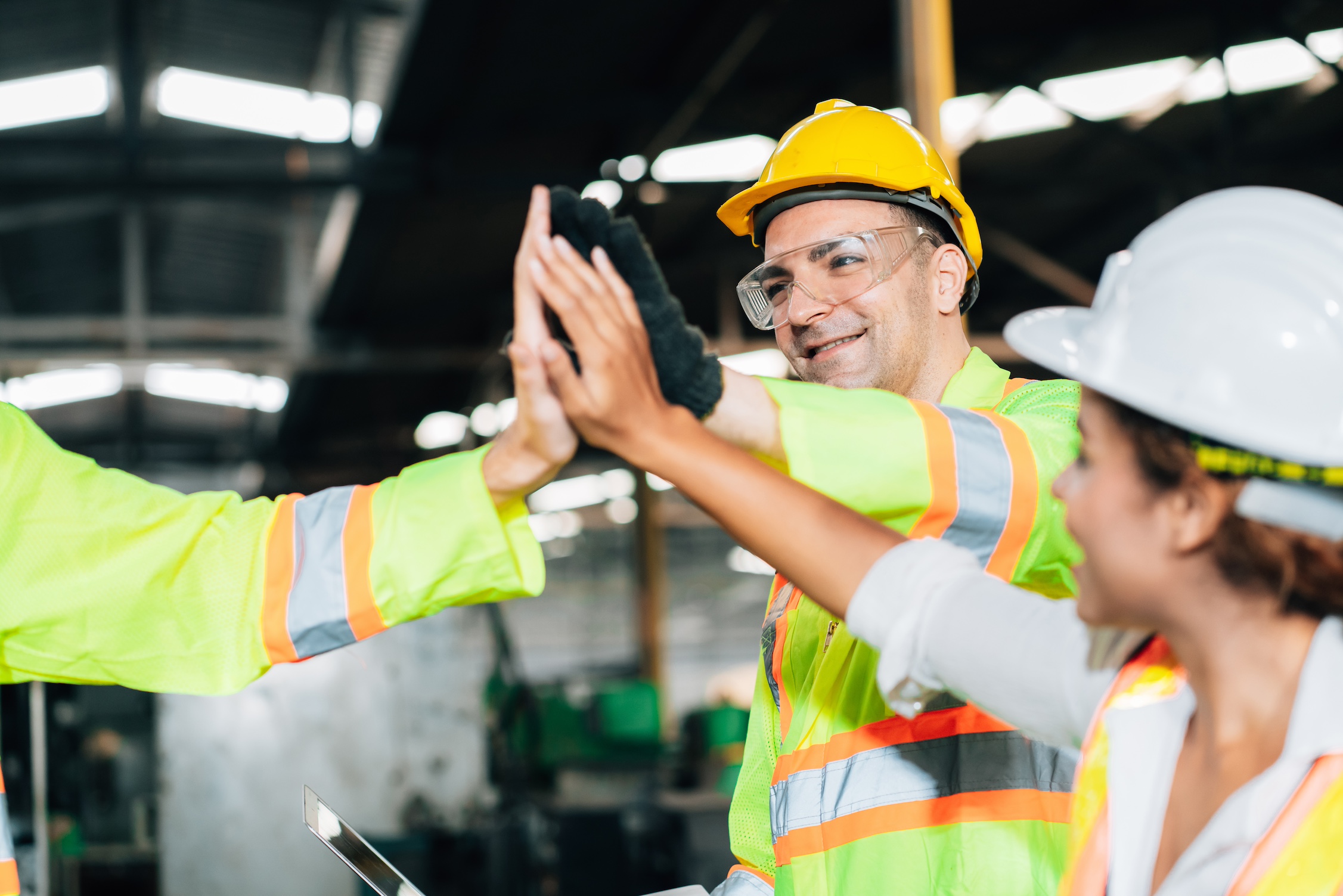
Benefits of a Well-Executed Preventive Maintenance Program
Numerous tangible benefits can significantly impact a manufacturing operation’s overall performance and efficiency. These benefits include cost savings, increased productivity, and enhanced asset longevity.
By preventing equipment failures before they occur, preventive maintenance helps in reducing the costs associated with emergency repairs and unscheduled downtime. A recent study by Jones Lang LaSalle highlighted that a telecommunications company saw a 545% return on investment (ROI) when implementing a preventive maintenance plan. The proactive approach allows businesses to manage their maintenance budgets more effectively and avoid the high expenses related to reactive maintenance.
Increased Productivity
Preventive maintenance ensures that equipment is always in optimal working condition, leading to fewer breakdowns and interruptions in production. This increased reliability means that production schedules can be met consistently, boosting overall productivity. Regular maintenance also allows maintenance teams to focus on planned activities rather than emergency repairs, further enhancing operational efficiency.
Enhanced Asset Longevity
Regular inspections and upkeep extend the lifespan of equipment by keeping it in good condition. This not only delays the need for costly replacements but also maximizes the return on investment for each asset. Preventive maintenance helps maintain the value of equipment and ensures it operates at peak performance for a longer period of time.
Implementing Your Preventive Maintenance Plan
Here are some tips and best practices for rolling out your preventive maintenance plan, including training, implementation, and adjusting strategies based on performance. Rolling out a preventive maintenance plan requires careful planning and execution to ensure a successful implementation:
- Comprehensive Training: Train your maintenance team on the new preventive maintenance procedures and any associated software tools, such as a CMMS. Ensure that all team members understand their roles, the importance of following checklists, and how to document their work accurately.
- Pilot Program: Consider starting with a pilot program, focusing on the most critical assets. This allows you to test the plan, identify any issues, and make necessary adjustments before a full-scale rollout.
- Clear Communication: Communicate the details of the preventive maintenance plan to all stakeholders, including management and maintenance staff. Ensure everyone is aware of the goals, procedures, and expectations associated with the plan.
- Monitor and Adjust: Continuously monitor the performance of the preventive maintenance plan using key performance indicators (KPIs). Use software to collect data on task completion, equipment performance, and any issues that arise. Use this data to make informed adjustments to the plan as necessary.
- Regular Reviews: Schedule regular reviews of the preventive maintenance plan to assess its effectiveness and make improvements. Involve all stakeholders in these reviews to gather feedback and ensure the plan evolves with your operations’ changing needs.
Measuring Success: KPIs and Metrics for Preventive Maintenance
To evaluate the success of your preventive maintenance efforts, it is essential to monitor relevant key performance indicators (KPIs). Some important KPIs to consider include:
- Mean Time Between Failures (MTBF): MTBF measures the average time between equipment failures. A higher MTBF indicates that equipment is running reliably, and preventive maintenance effectively reduces failures.
- Mean Time to Repair (MTTR): MTTR measures the average time to repair equipment after a failure. A lower MTTR indicates that repairs are being completed quickly, minimizing downtime.
- Preventive Maintenance Compliance: This KPI measures the percentage of preventive maintenance tasks completed on schedule. High compliance rates indicate that the maintenance plan is being followed effectively.
- Overall Equipment Effectiveness (OEE): OEE measures the overall performance of equipment by considering availability, performance, and quality. A higher OEE indicates that equipment is operating efficiently and producing quality output.
- Maintenance Costs: Track the costs associated with preventive and corrective maintenance. A well-implemented preventive maintenance plan should reduce overall maintenance costs over time.
Customizing Preventive Maintenance Plans with CMMS
Using a CMMS to customize features and tailor preventive maintenance schedules and tasks to fit unique business needs. Each piece of equipment in your inventory has unique maintenance requirements. A CMMS allows you to create asset-specific maintenance plans that consider the manufacturer’s recommendations, historical performance data, and asset criticality to operations. By customizing maintenance tasks and schedules for each asset, you ensure that maintenance is precisely aligned with the needs of your equipment.
CMMS software offers flexible scheduling options, including time-based, usage-based, and condition-based maintenance triggers. This flexibility allows you to choose each asset’s most effective scheduling method.
- Time-based scheduling ensures maintenance tasks are performed regularly (e.g., monthly, quarterly), while usage-based scheduling triggers maintenance after certain operational hours or cycles.
- Condition-based maintenance uses real-time sensor data to trigger maintenance when specific conditions are met (e.g., temperature thresholds and vibration levels).
Customizing work orders in a CMMS can streamline maintenance operations. You can set up automated work orders that are generated and assigned to technicians based on predefined triggers. This ensures that maintenance tasks are not overlooked and are completed on time. Additionally, work orders can include detailed instructions, checklists, and necessary tools and parts, improving the efficiency and consistency of maintenance activities.
A CMMS allows you to optimize resource allocation by assigning tasks to technicians based on their skills, availability, and location. This ensures that the right personnel perform the right tasks at the right time. Customizing resource allocation helps balance the workload and improves overall maintenance efficiency.
Customizable reporting provides insights into maintenance performance. You can generate reports on various KPIs, such as maintenance compliance, mean time between failures (MTBF), and mean time to repair (MTTR). These insights help you identify trends, monitor progress, and make data-driven decisions to continuously improve your preventive maintenance plan.
Overcoming Challenges in Preventive Maintenance Implementation
Businesses face some common obstacles when implementing preventive maintenance plans and strategies to overcome them, including:
- Resistance to Change: Employees may resist changes to established routines and processes. To overcome this, involve your maintenance team in the planning process from the beginning. Communicate the benefits of preventive maintenance, provide training, and address any concerns. Creating a culture that values proactive maintenance and continuous improvement can help ease the transition.
- Lack of Resources: Limited resources, including budget constraints and staffing shortages, can hinder implementing a preventive maintenance plan. To address this, prioritize critical assets and maintenance tasks that offer the most significant benefits. Use a CMMS to optimize resource allocation and track maintenance costs. Consider phased implementation, starting with a pilot program and gradually expanding as resources allow.
- Inaccurate Data: Accurate data is essential for effective preventive maintenance. Inaccurate or incomplete data can lead to suboptimal maintenance schedules and missed tasks. Implement robust data collection and management practices, including regular audits and updates to asset information. Use CMMS software to centralize data and ensure consistency across the organization.
- Scheduling Conflicts: Coordinating maintenance activities with production schedules can be challenging, especially in high-demand environments. To mitigate this, use a CMMS to plan maintenance tasks during periods of low production activity or scheduled downtime. Communicate maintenance schedules with production teams to minimize disruptions and ensure alignment.
- Measuring Effectiveness: It can be challenging to measure the effectiveness of a preventive maintenance plan without clear metrics and KPIs. Establish specific, measurable goals for your maintenance program, such as reducing downtime or increasing asset reliability. Use a CMMS to track and report on these KPIs and conduct regular reviews to assess progress and make necessary adjustments.
By customizing your preventive maintenance plan using CMMS features and addressing common implementation challenges, you can create a robust and effective maintenance strategy that enhances operational efficiency, reduces costs, and extends the lifespan of your assets. Reach out for more information and for a demo of our CMMS today!