Effective asset lifecycle and equipment management is crucial, and preventive maintenance is the first step. By proactively servicing equipment to prevent failures before they occur, manufacturers can ensure optimal performance, minimize downtime, and maintain compliance with industry regulations.
Preventive Maintenance vs. Reactive Maintenance
Preventive maintenance stands in stark contrast to reactive maintenance, which addresses issues only after they arise. While reactive maintenance may seem like a straightforward approach, it often leads to unexpected downtime, costly repairs, and disruptions to production schedules. In contrast, preventive maintenance involves scheduled inspections, repairs, and replacements designed to identify and address potential issues before they escalate into major problems.
The Importance and Benefits of Preventive Maintenance Schedules
Implementing preventive maintenance schedules offers a number of benefits for manufacturers, including:
- Minimized Downtime: Preventive maintenance helps minimize unplanned downtime by proactively identifying and addressing potential issues, ensuring continuous operation and production efficiency.
- Extended Equipment Lifespan: Regular maintenance tasks, such as lubrication, calibration, and cleaning, can significantly extend the lifespan of equipment, reducing the need for costly replacements and downtime-inducing repairs.
- Enhanced Safety: Regular maintenance not only ensures equipment reliability but also promotes workplace safety by identifying and addressing potential safety hazards before they pose a risk to employees.
- Improved Compliance: Compliance with industry standards and regulations is non-negotiable in regulated industries. Preventive maintenance schedules help regulated manufacturers stay compliant by ensuring that equipment meets regulatory requirements and operates within specified parameters.
- Cost Savings: While preventive maintenance requires an upfront investment of time and resources, it ultimately leads to significant cost savings by preventing costly breakdowns, reducing repair costs, and optimizing equipment performance.
Preventive maintenance schedules promote equipment reliability, safety, compliance, and cost-effectiveness. They allow manufacturers to enhance efficiency, mitigate risks, and maintain a competitive edge in the regulated manufacturing landscape.
Developing an Effective Preventive Maintenance Schedule
With the right approach and tools, creating an effective preventive maintenance schedule is entirely manageable. Before jumping into the practical steps of creating a preventive maintenance schedule though, it’s essential to grasp the concept and significance of preventive maintenance itself.
As we touched on, unlike reactive maintenance, which addresses issues after they occur, preventive maintenance focuses on proactively servicing equipment to prevent failures before they happen. At its core, a preventive maintenance schedule is a structured plan outlining maintenance tasks scheduled at specific intervals or triggers, such as time-based, usage-based, condition-based, or predictive maintenance.
Steps to Create a Robust Preventive Maintenance Schedule
Begin by identifying and prioritizing critical assets crucial to business operations. Consider factors such as equipment importance, failure modes, repair costs, and likelihood of failure over time. This ensures that resources are allocated effectively to maximize returns.
Determine the most suitable maintenance triggers for your assets, whether it’s time-based, usage-based, condition-based, or predictive. Leverage data and modern Computerized Maintenance Management System (CMMS) to automate scheduling and integrate with condition monitoring systems for predictive maintenance strategies.
Not all maintenance tasks are equal in urgency and importance. Prioritize tasks based on asset criticality, safety risks, operational disruptions, and resource requirements. This helps with efficient resource allocation and decision-making.
Clear task assignments ensure accountability and streamline task execution. Consider factors like skill level, asset location, and operational disruptions when assigning responsibilities. This fosters a culture of ownership and ensures timely task completion.
Preventive maintenance checklists are helpful. Documentation is key to effective maintenance, after all. Implement preventive maintenance checklists to ensure consistent and thorough task completion. Modern CMMS systems streamline documentation processes, saving time and enhancing accuracy.
Then, regularly evaluate the performance of your preventive maintenance schedule using metrics like MTBF, PMP, and PMC. Identify areas for improvement and adjust schedules accordingly to optimize performance continually.
Streamlining Operations With a Computerized Maintenance Management System (CMMS)
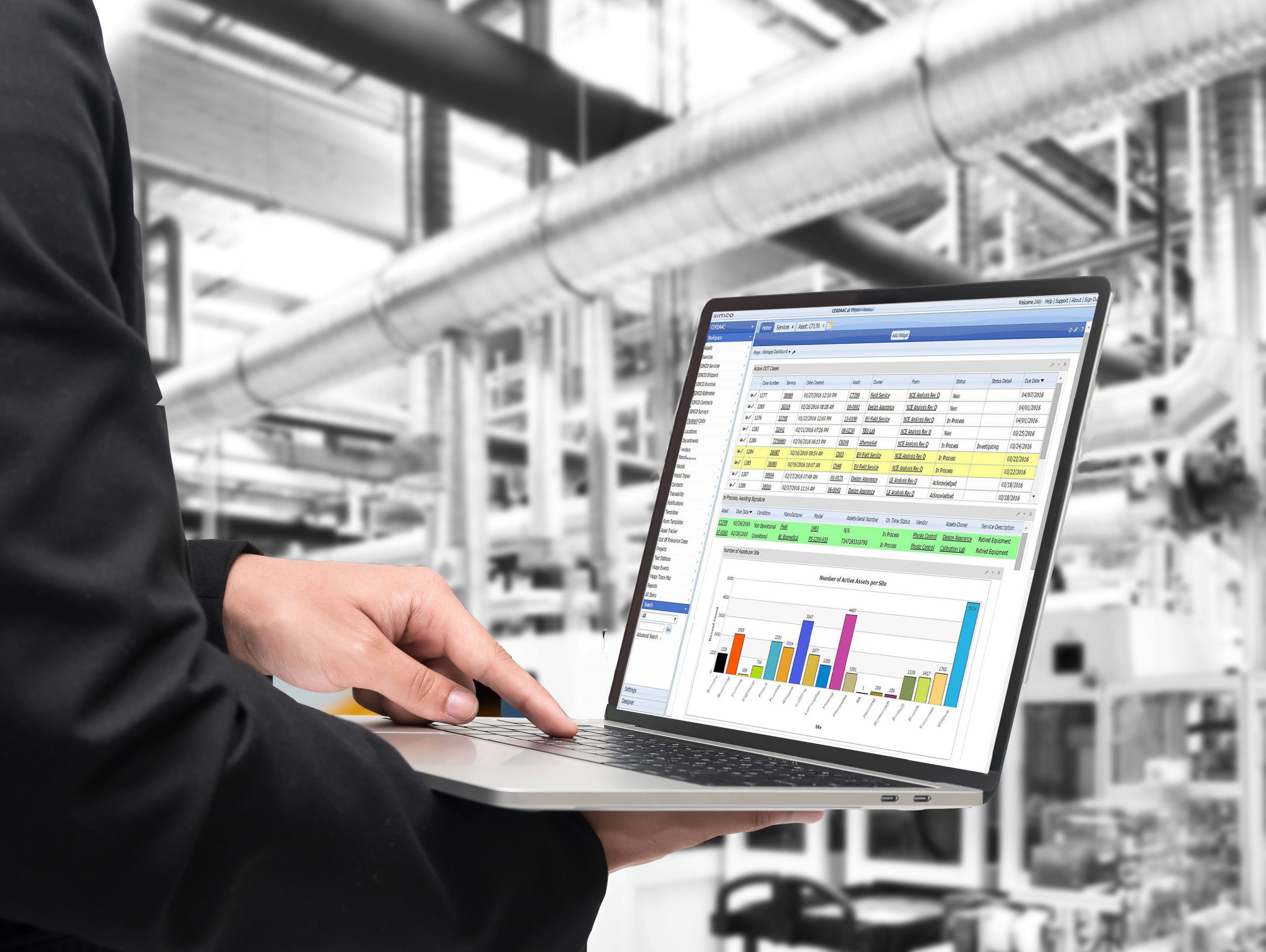
A CMMS offers a comprehensive solution for manufacturers seeking to streamline their preventive maintenance processes. With features designed to enhance efficiency and compliance, a CMMS empowers manufacturers to:
- Prioritize assets based on criticality and compliance requirements.
- Automate scheduling and task assignments for streamlined execution.
- Ensure accountability and documentation with comprehensive audit trails.
- Leverage performance metrics and analytics for data-driven decision-making.
- Maintain compliance with regulatory standards with audi-ready documentation
The additional complexity of regulated environments demands sophisticated technological solutions. Both CMMS and Enterprise Asset Management (EAM) software enhance preventive maintenance scheduling by providing centralized platforms for managing assets, scheduling maintenance tasks, and tracking maintenance activities. Here’s how:
- Centralized Asset Management: Allows regulated manufacturers to create a comprehensive database of assets, including equipment specifications, maintenance history, and compliance documentation, ensuring visibility and traceability across the organization.
- Streamlined Scheduling: Preventive maintenance schedules can be easily created, customized, and managed. Maintenance tasks can be scheduled based on time-based triggers, usage-based triggers, or condition-based triggers, ensuring that critical equipment receives timely attention.
- Resource Optimization: By prioritizing assets based on criticality and resource requirements, software helps regulated manufacturers optimize resource allocation and maximize operational efficiency.
The Benefits of Automation and Real-Time Data Tracking
Automation and real-time data tracking are integral components of modern preventive maintenance strategies and help optimize operations with features like:
- Automated Scheduling: By automating preventive maintenance scheduling, manual processes can be eliminated and the risk of human error is significantly reduced. Automated scheduling ensures that maintenance tasks are performed on time, minimizing the likelihood of equipment failures and associated downtime.
- Real-Time Monitoring: This allows maintenance teams to monitor equipment performance in real-time, detecting issues as they arise and taking proactive measures to address them. Real-time monitoring enables a level of predictive maintenance, where maintenance tasks are triggered based on equipment condition data, further reducing the risk of unplanned downtime.
- Data-Driven Decision-Making: The software provides valuable insights into equipment performance, maintenance trends, and compliance status through advanced reporting and analytics capabilities.
Manufacturers can leverage this data to make informed decisions, optimize maintenance strategies, and demonstrate compliance to regulatory authorities.
And among the various CMMS/EAM solutions available, CERDAAC stands out as a comprehensive platform designed specifically for manufacturers. It supports creating and managing preventive maintenance schedules, with automated scheduling complete with triggers, such as time intervals or equipment usage, ensuring that maintenance tasks are performed at the right time.
There are customizable checklists for each maintenance task, ensuring thorough and consistent execution. These checklists can be tailored to specific regulatory requirements and organizational standards. And real-time access to data helps maintenance teams monitor equipment performance and maintenance activities, enabling timely intervention and proactive maintenance.
You’ll also find robust reporting capabilities, allowing users to generate detailed reports on maintenance activities, compliance status, and equipment performance. These reports facilitate regulatory audits and continuous improvement initiatives.
But regardless of the software you select, there are best practices to keep in mind when creating your preventative maintenance plan.
Recommendations for Maintaining an Effective Preventative Maintenance Schedule
Technology adoption is a given, as you’ll want to leverage features such as automated scheduling, customizable checklists, and reporting capabilities to enhance efficiency and compliance.
Invest in training programs to ensure that maintenance personnel are proficient in using your CMMS/EAM software and executing preventive maintenance tasks effectively. Ongoing training to keep employees updated on industry best practices, regulatory requirements, and technology advancements is also important.
Continuously monitor and analyze key performance indicators (KPIs) related to preventive maintenance, such as mean time between failures (MTBF), preventive maintenance compliance (PMC), and overall equipment effectiveness (OEE). And use data-driven insights to identify trends, address performance issues, and optimize maintenance strategies now and in the future.
Evolving Preventative Maintenance Practices
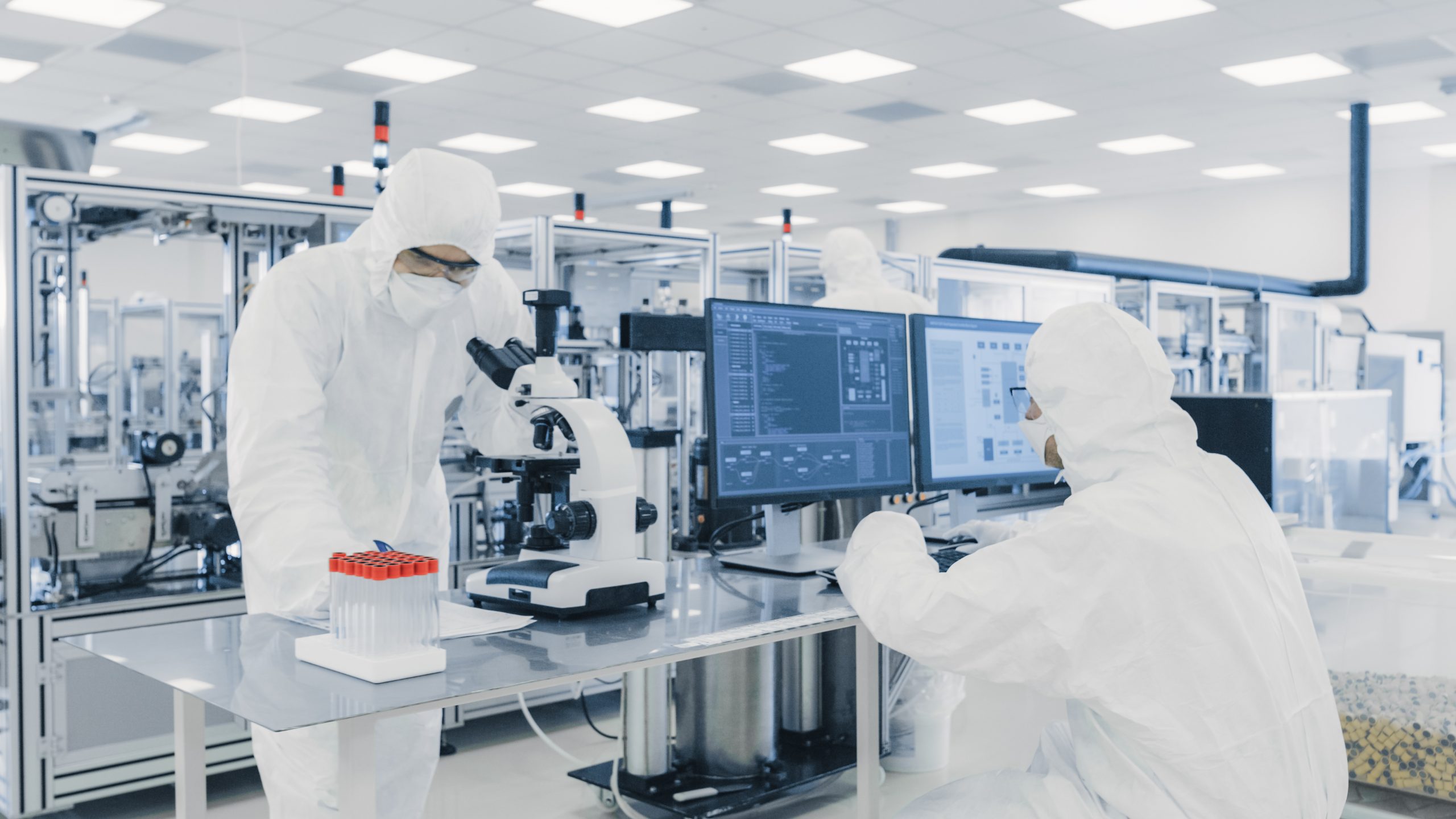
Adopting evolving preventive maintenance practices is crucial. These practices not only ensure operational efficiency but also contribute to sustainability goals and regulatory compliance.
Integration with IoT
The Internet of Things (IoT) has revolutionized the way manufacturers approach maintenance. By integrating preventive maintenance schedules with IoT devices, manufacturers gain access to real-time asset condition monitoring, enabling proactive maintenance interventions. IoT sensors embedded in equipment can continuously monitor parameters such as temperature, vibration, and performance metrics.
Any deviations from predefined thresholds trigger alerts, prompting maintenance teams to take corrective action before issues escalate. This predictive maintenance approach minimizes downtime, reduces the risk of unplanned breakdowns, and extends equipment lifespan. Moreover, by harnessing IoT data, manufacturers can optimize maintenance schedules, improve resource allocation, and enhance overall operational efficiency.
Sustainability Impact
In today’s environmentally conscious world, sustainability is a key focus for manufacturers. Preventive maintenance plays a vital role in sustainability efforts by reducing waste, minimizing resource consumption, and improving energy efficiency. By ensuring equipment operates at peak performance levels, preventive maintenance prevents unnecessary wear and tear, reducing the need for premature replacements and minimizing material waste.
Additionally, optimized equipment reduces energy consumption, lowers carbon emissions, and contributes to a greener manufacturing process. By aligning preventive maintenance practices with sustainability goals, regulated manufacturers can demonstrate their commitment to environmental stewardship while reaping tangible benefits in terms of cost savings and brand reputation.
Regulatory Compliance
Compliance with industry regulations and standards is non-negotiable for regulated manufacturers. Preventive maintenance is crucial in helping organizations maintain assets in optimal condition, ensuring compliance with regulatory requirements.
By adhering to prescribed maintenance schedules and performing routine inspections, manufacturers can mitigate risks associated with equipment failures and safety hazards. And robust preventive maintenance practices provide documentation of maintenance activities, which is essential during regulatory audits and inspections.
By staying proactive and preemptively addressing potential compliance issues, manufacturers can avoid penalties, safeguard their reputation, and maintain a competitive edge in the market.
Evolving preventive maintenance practices are essential for manufacturers seeking to keep pace with their competitors. This means they must optimize operational efficiency, drive sustainability initiatives, and ensure regulatory compliance.
And as technology continues to advance and industry standards evolve, adopting proactive preventative maintenance strategies will be vital to staying competitive and achieving long-term success. Connect with us for a demo of CERDAAC’s CMMS capabilities and to see what the future has in store for your manufacturing operation!